对于金属材料,服役对象材料性质与零件性能之间存在正相关特性,为制备高强高韧金属材料和长寿命金属服役零部件,研究者们在不断致力于新材料研发工作的同时,对材料微观组织状态的研究也从宏观、介观尺度不断深入到微纳尺度[1−2]。实际应用中,评判零部件使用寿命的重要因素之一是零件疲劳性能的稳定性,而影响零件疲劳性能稳定性的主要因素是制造和服役过程中组织性能的均匀性和稳定性。一方面,材料在制造加工过程中由于不同部位不均匀受力或受热致使材料内部产生残余应力;另一方面,由于制造加工过程形变相变不均匀,易造成零件基体损伤与缺陷波动,如应变硬化、位错塞积、应力集中、成形缺陷等。当零件中残余应力在特定服役条件下与外力耦合,会改变零件的实际受力状态,易造成零件服役早期发生局部微区损伤缺陷区域失效,引起零件失效,最终导致其疲劳性能不稳定、离散度大。为了解决这类问题,采用时效技术,如自然时效(Natural stressrelief, NSR)以及人工时效 (Artificial stress relief,ASR) [3−8],其中人工时效主要包括时效热处理(Thermal stress relaxation, TSR)和振动时效(Vibration stress relief, VSR),可在一定程度上有效地提升零件使用性能和疲劳寿命[9−10],TSR和VSR技术己在工业上获得广泛应用,但实际应用过程中仍存在明显不足。例如,时效热处理(TSR)的局限性主要体现在如下两个方面:一方面,热处理设备费用较高,能源消耗大;另一方面,构件可能出现热处理变形的问题,同时也可能引入新的残余应力[11−14]。振动时效(VSR)的局限性则主要体现在,对零件进行整体时效处理时局部振动应力过大易引起构件疲劳破坏[15−16]。
电磁脉冲处理是一种新型加工技术,具有绿色无污染、效率高等优势。其采用接触式或非接触式交变脉冲电流或脉冲磁场作用于材料局部或者整体区域,利用电磁脉冲在短时间内与材料微观组织和缺陷发生相互作用,通过脉冲电流或脉冲磁场产生的热效应和非热效应以及两者耦合效应来改善材料微结构,提高材料力学性能或提升其使用性能。因此,电磁脉冲处理技术已经广泛用于辅助成型制造[17−19]、辅助加工制造[20−21]、辅助热处理[22−23]及电磁冲击强化[24−25]等研究。
由于电磁脉冲作用于金属材料时多场耦合的复杂性,其影响材料组织性能的微观作用机理目前还没有统一的观点。目前学者们普遍认为这是多种效应复合作用的结果,包括焦耳热效应[26−27],电子风力作用[28]和磁致伸缩效应[29]等,尤其与金属内部位错的运动密切相关[30−32]。同时,电磁脉冲对金属材料的影响具有“局部针对性”或者“选择性作用”特征[33−34],合金内部不同状态的微区,对于电磁脉冲能量的响应往往不同。本文作者近期研究表明[35],在近室温条件下,电磁脉冲对合金晶粒会产生微振动效应,合金不同位置处会发生非线性弹塑性变形,可调整如微织构、愈合微裂纹等微观损伤,同时,对合金微观缺陷,如空位、杂质原子、位错、晶界和相界等产生非线性激励作用,达到调控残余应力和修复微纳尺度损伤缺陷的目的。这启发作者,可将电磁脉冲处理技术应用到调控成品金属零件残余应力中,即将电磁脉冲的微振动效应及焦耳热效应进行有效结合,达到热振复合时效工艺效果,为提高零件使用性能一致性和稳定性,进而提升零件疲劳寿命提供一种新思路。
TC11钛合金最早是 20 世纪 50 年代中期由美国Crucible 公司研制出的一种新型抗氧化、超高强钛合金,具有良好的抗氧化性能、优良的冷热加工性能、较高的力学性能以及良好的环境抗力,已经用于制造航空发动机叶片[36−37]。但目前,TC11钛合金叶片使用性能和疲劳寿命还有待提升。已有文献表明,电磁场复合调控处理可通过基体微区形变相变改善叶片表层残余应力分布,从而有效提升航空发动机钛合金叶片的疲劳极限强度[38],但关于电磁场复合调控处理提升钛合金叶片疲劳极限的物理机制,仍需开展更为深入的实验与理论研究。本文将利用电磁脉冲能量对TC11钛合金叶片进行电磁冲击试验,调控叶片整体残余应力分布,提升成品叶片疲劳极限,同时,结合有限元仿真分析,针对电磁冲击处理对TC11钛合金叶片疲劳性能的影响机理进行进一步探讨。
1、 实验与仿真
1.1 实验研究
实验选用喷丸后的 TC11钛合金叶片成品件进行电磁冲击试验。采用自制的电磁冲击装置对TC11钛合金叶片进行电磁冲击试验,电磁冲击装置示意图如图 1(a)所示。试验主要工艺参数如表1所示,电磁冲击过程中使用FOTRIC 226红外热像仪监测叶片表面温度变化情况,结果如图 1(b)所示,试验过程中试样表面最高温度未超过 60 ℃。
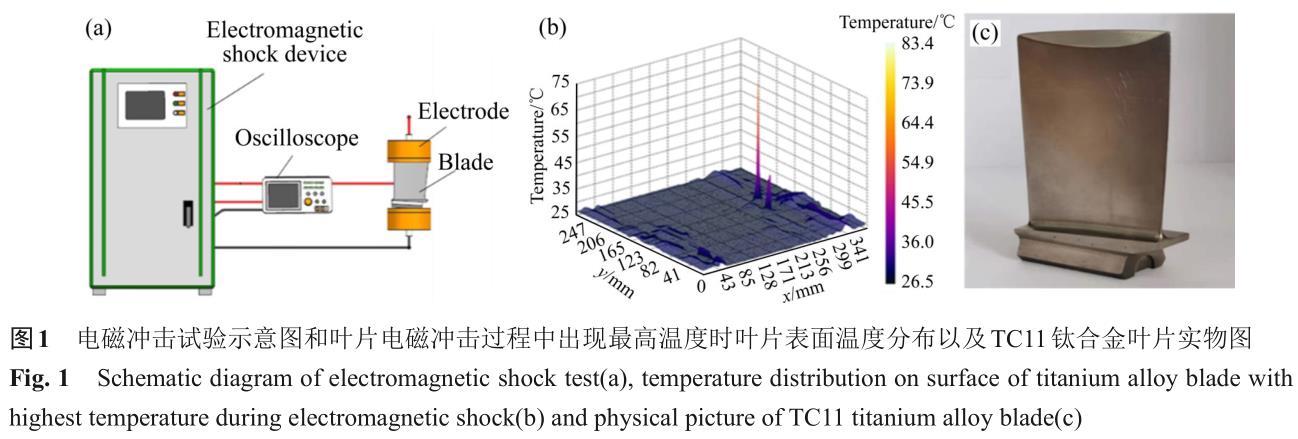
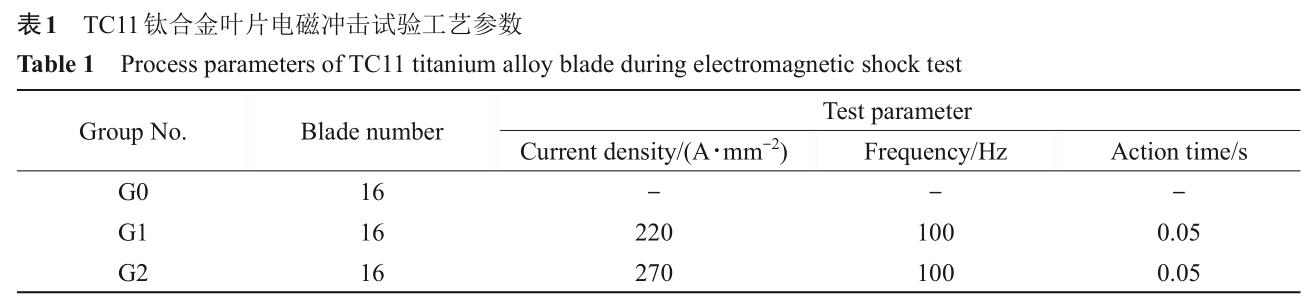
电磁冲击试验结束后,取未处理叶片组(G0)和电磁冲击处理后叶片组(G1和G2)中的1#~15#叶片用于振动疲劳测试,16#叶片用于残余应力测试。
采用激振技术,依据航标《发动机叶片及材料振动疲劳试验方法》(HB 5277—84),结合升降法对一组(15个)TC11钛合金叶片进行振动疲劳测试。对未处理叶片和经电磁冲击处理后的叶片采用X射线残余应力检测仪(XSTRESS 3000)测定钛合金叶片叶背表层残余应力,并通过剥层法实现不同深度残余应力测试。试件电解经剥层完毕后,正面用水清洗,腐蚀区域用丙酮清洁,去除表面杂质,再用酒精擦拭,热风吹干,使其达到应力测量要求的光洁度。等试样表面完全干燥后,在腐蚀区域利用事先制备的定位板卡标示出应力测量的点,以确保逐层定点应力测量。应力测试条件如下:Ti靶,管压30kV,管流6.7mA,曝光时间5s。
不同电磁冲击工艺处理的TC11钛合金叶片在经振动疲劳失效后,从未处理叶片组和电磁冲击处理后叶片组振动疲劳测试(1#~15#)叶片中取出对应最大失效强度的叶片进行显微硬度测试和裂纹形貌观察。采用线切割将疲劳失效后叶片沿中部对称剖开,如图2(a)所示;利用透明环氧树脂对叶片试样进行镶样,如图2(b)所示。采用 HVS−1000 硬度计测试上述叶片剖面维氏硬度分布,测量载荷为1.96N,保压时间为10s。硬度测量取点位置:纵向上,分别在试样表面以距左侧底平面4 mm处为起始点,每隔5 mm取点;横向上,分别在叶片剖面中心处、距叶背0.5 mm处和距叶盆0.5 mm处取点,取平均值,如图2(b)所示。
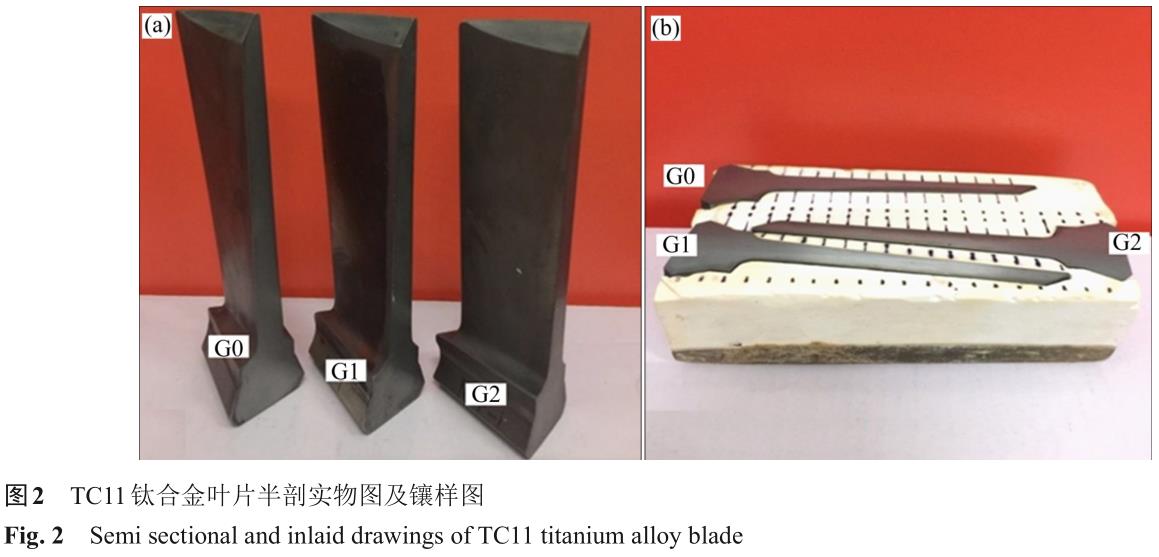
同时,从未处理叶片组和电磁冲击处理后叶片组用于残余应力测试(16#)的叶片中取样进行显微显微组织观察。对试样进行打磨至表面光滑,再在抛光机上进行抛光至表面光亮,用酒精擦洗干净后采用腐蚀液 (5.0% HF+15.0% HNO3+80.0% H2O,体积分数) 进行腐蚀。采用蔡司金相显微镜(ZeissScope A1)和扫描电镜(ZEISS AURIGA)对各试样的显微组织和裂纹分布进行观察。
1.2 仿真模拟
为分析叶片疲劳性能提升的原因,分别使用DEFORM及ANSYS软件对叶片制造成形及服役阶段的应力状态进行分析。首先对叶片进行几何建模及网格划分,由于钛合金叶片叶身部分是闭合双曲面变截面结构,为简化叶片几何模型,建立以叶片长度方向中部纵截面为基准的等截面叶片几何模型;在此基础上,对锻件坯料采用四面体网格划分,叶片长度约为90mm、叶身宽度约为40mm。为了能够更加真实、准确地反映叶根部位在热锻、热处理及服役过程中的实际变化情况,对叶根部位的网格进行局部加密,网格模型见图3。
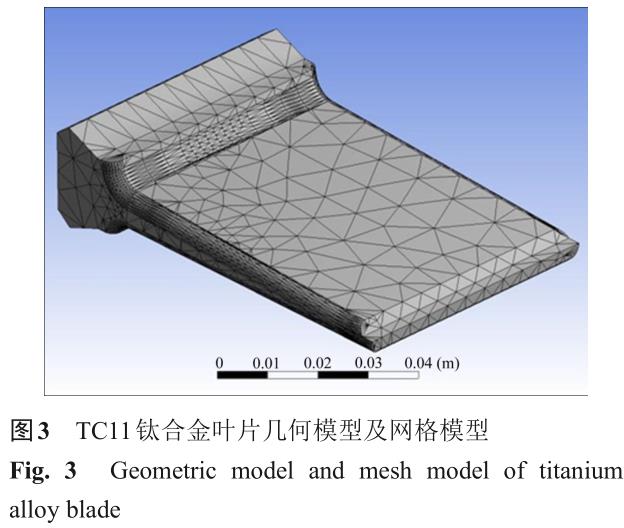
材料选用国产TC11(Ti-6.5Al-3.5Mo-1.5Zr-0.3Si)钛合金,其部分物理属性见表2。仿真模拟的初始条件及边界条件设置如下:锻造过程中 ,TC11钛合金一般在(α+β)两相区进行锻造,锻件坯料的加热温度根据钛合金β 相变点进行设定,坯料加热温度设定为940 ℃[39],模具温度为200 ℃,锻造过程中设定停止条件为上、下模具完全闭合,设定每次压下步进量,要求保证最小网格在每次压下过程中发生塑性变形;热处理过程中,需对锻造后的叶片坯件进行退火处理,首先将叶片加热至(550±10) ℃保温1 h,随后在 (850±10) ℃保温6 h后空冷;叶片服役阶段,对叶片表面施加均匀分布的等压空气应力,同时设置工件的初始温度为20 ℃;服役过程中,结合叶片实际服役状态,约束底面结点的6个自由度来固定叶片。

2、 实验结果
2.1 电磁冲击对叶片振动疲劳极限强度的影响
对不同电磁冲击工艺处理的 TC11钛合金叶片进行振动疲劳测试,根据图 4(a)~(c)测试结果,依据航标HB 5277—84计算叶片疲劳极限强度,结果如图4(d)所示。未处理以及经不同工艺参数电磁冲击处理后叶片的疲劳极限强度分别为 492、528 和672 MPa。电磁冲击处理后,TC11钛合金叶片的疲劳极限发生了不同程度的改善,分别提升7.3% 和36.6%,电磁冲击处理在控制温升较低以及作用时间极短的情况下对钛合金叶片的疲劳性能起到较为显著的提升作用。
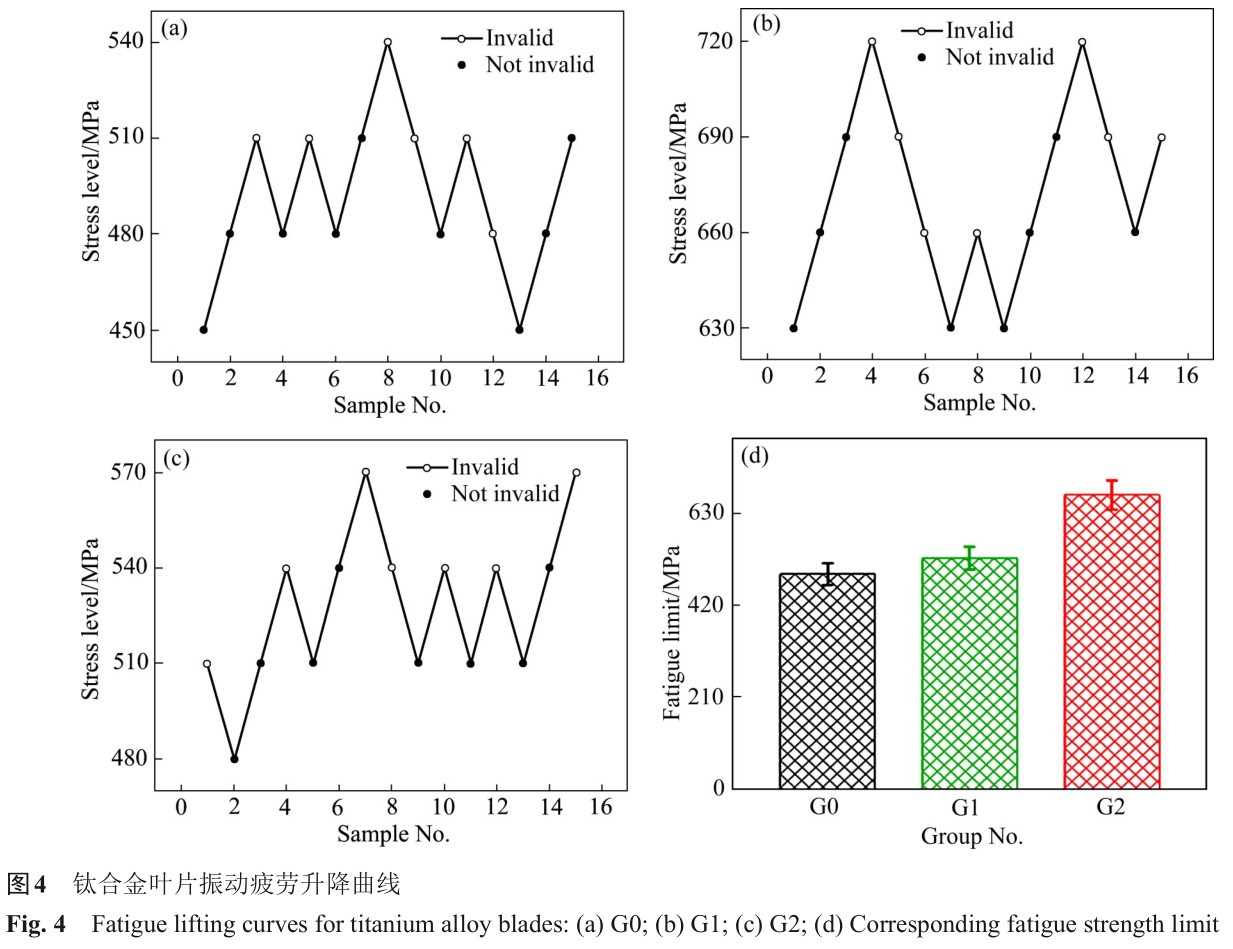
从各疲劳测试组中取出最大失效强度的叶片进行分析,对叶片裂纹进行金相观察,结果如图5所示。结果表明,未处理叶片G0和经电磁冲击处理叶片 G1,裂纹位于叶背面的叶身根部圆角处,而电磁冲击处理叶片 G2,裂纹则位于叶背上。进一步的测量表明,未处理叶片G0和经电磁冲击处理叶片G1,其裂纹距叶榫底面的距离分别为 17.0 和17.2 mm,而经电磁冲击处理G2叶片,其裂纹距叶榫底面的长度为21.0mm。未处理叶片 G0 和经电磁处理叶片 G1、G2的裂纹深度分别为28.0、14.0和13.0mm。这表明经电磁冲击处理后,叶片失效后的裂纹位置和裂纹深度均发生了变化。

2.2 电磁冲击对叶片表层残余应力及剖面硬度分布的影响
针对不同工艺处理的 TC11钛合金叶片,采用X射线衍射法测定钛合金叶片表层残余应力,并通过剥层法实现不同深度残余应力测试,其结果如图6所示。经不同电磁冲击处理后,随着峰值电流密度的增大,叶片表层残余压应力增大。表层残余压应力的增加,不仅可以抵消疲劳应力,而且可以抑制微裂纹的产生和扩展,从而提升材料疲劳寿命[40]。因此,初步推测电磁冲击处理可以通过提升叶片表层残余压应力来提升叶片疲劳寿命。
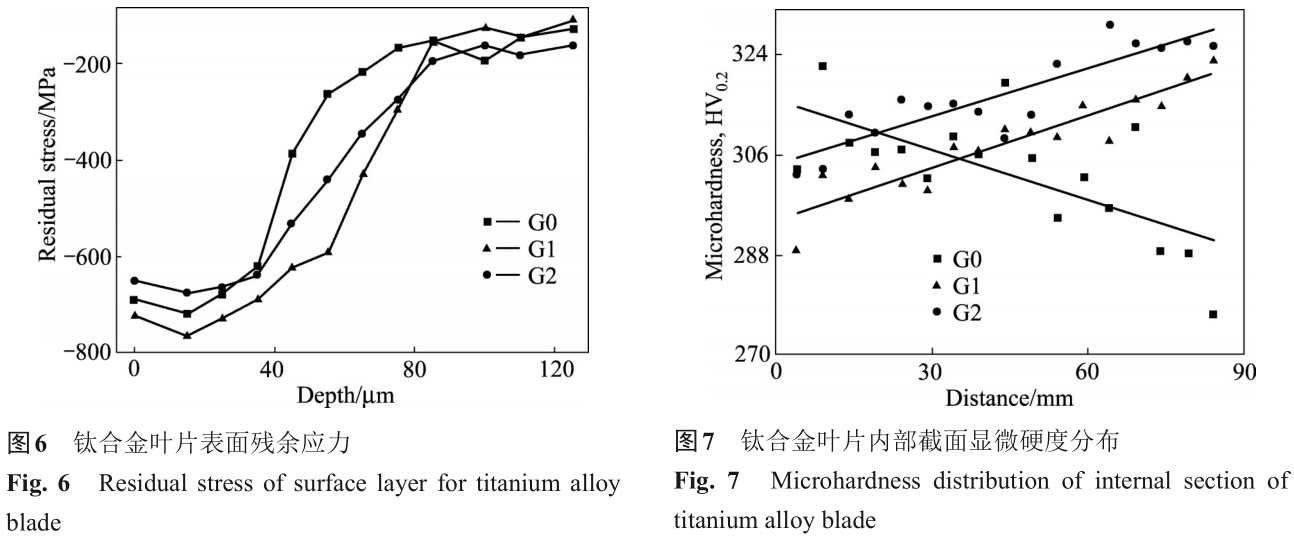
图7所示为叶片剖面显微硬度测试结果。结果表明,叶片显微硬度分布发生了明显的变化,未处理叶片,靠近叶榫端硬度较高,远离叶榫端硬度下降,而处理后这一趋势则相反;其次,经电磁冲击处理后,叶片显微硬度也有略微提升,硬度均值由302.8HV(G0) 分 别 提 升 至 308HV(G1) 和 316.8HV(G2),叶片剖面显微硬度测试结果表明,电磁冲击处理不仅调控了叶片表层残余应力,也可调控叶片内部的残余应力大小和分布。
2.3 电磁冲击对叶片剖面显微组织及失效裂纹的影响
图 8(a)所示为未处理 TC11钛合金叶片的金相组织,经不同参数电磁冲击处理后的微观组织形貌如图 8(b)和(c)所示。图 8 中白色组织为 α 相,黑色组织为β相。由图8可知,未处理试样和经电磁冲击处理试样的金相显微形貌未见明显变化,均为等轴组织,各相尺寸以及体积分数也基本保持不变。

在金相组织未见明显变化的基础上,为了进一步分析电磁冲击作用下钛合金微结构的演化及其对钛合金疲劳性能的影响,对失效后的钛合金叶片产生裂纹部位取样进行扫描分析,其裂纹终端分布情况如图9所示,可见经过电磁冲击处理的钛合金叶片裂纹源形貌优于未处理叶片;而且,对比分析图9(a)~(c)可知,钛合金相组织扫描形貌图也未见明显变化。
以上结果表明,电磁冲击作用下叶片显微组织未见明显变化,但叶片表层残余应力分布及内部硬度分布变化较大,由此推测,电磁冲击对叶片整体内应力的调控,可能是其提升叶片振动疲劳极限的主要原因之一。下文将结合仿真分析,从电磁冲击对叶片内应力影响的角度探讨电磁冲击处理对叶片振动疲劳极限的影响。
3、 叶片残余应力有限元仿真分析
叶片成形过程中材料会发生不均匀塑性变形及相变,引发应变不相容从而产生应力演化。叶片加工过程中残余应力会随着加工余量脱离本体而被部分释放,原始残余应力自平衡状态被破坏并发生再平衡,甚至,局部产生的高热会导致表层形成新的残余应力梯度。叶片真空退火保温过程通常位于制造过程的后端,虽通过回复和可能发生的蠕变释放部分残余应力,但高温退火的加热和冷却过程中,其横截面的温度梯度较大,由此产生较大的热应力,同时,冷却时合金组织中亚稳β相又会析出次生α相,尽管热处理前后组织比容差不大,但仍会产生一定的组织应力,可见,叶片热处理过程残余应力的演化较为复杂、影响较为活跃,是残余应力控制的关键[41],在后续使用过程中与外载荷相叠加,进而影响后续的机加工过程及服役行为,即使后续喷丸强化处理可改善叶片表面的残余应力状态,但其影响层厚度通常只有百微米左右。
因 此 , 在 实 验 研 究 的 基 础 上 , 本 文 采 用DEFORM 软件分别模拟计算了钛合金叶片锻坯在热锻过程中应力随时间的变化规律和热处理过程中温度场随时间的变化规律,同时,采用ANSYS软件模拟计算了叶片服役过程中应力随时间的变化规律,分析了叶片成形过程及热处理过程中内应力变化对其服役过程疲劳失效可能产生的影响。
在热锻初期,叶片变形从叶榫开始逐渐向叶身推进,叶榫及叶根处坯料在锻压力的作用下,向叶身流动,如图 10(a)所示;同时,在热锻过程中,叶片锻坯在不断变薄、变平滑时,从叶榫、叶根到叶身部位的应力呈非均匀分布趋势,如图10(b)~(c)所示;尤其是叶根成形过程中两侧的坯料不断受挤压,如图 10(d)所示,热锻结束后,叶片根部容易形成如微织构、局部应力集中等微观损伤,该机械损伤在后续热锻过程中会延伸至叶根内部并被两侧坯料覆盖,最终导致叶根部位组织性能稳定性较差,对叶片服役性能产生较大负面影响。为提高叶片锻坯的力学性能,需对其进行热处理。图 11 所示为叶片热处理过程中叶片叶背表面中部(位置P1~P300处)温度分布模拟结果。由图11可以看出,热处理升温与降温过程中,钛合金叶片锻件叶背表面不同位置处的温度差别(Δθ)较大 (86~185.2 ℃)。在550 ℃退火处理加热阶段的某一时刻(t1)和 850 ℃退火处理加热阶段的某一时刻(t3),叶
根部位温度相对其周围基体温度为温度极小值点,叶根处叶片材料热膨胀量相对周围基体较小,不同位置处的最大温差分别为 130℃ 和 86℃;而在550 ℃退火处理和850 ℃退火处理的保温阶段,经过足够长时间的保温后的某一时刻(t2,t4),从叶片叶根到叶尖部分的温度分布是均匀的,不存在温差;最终,退火处理最终冷却阶段的某一时刻(t5),叶根部位温度相对其周围基体温度为温度极大值点,叶根处叶片材料冷却收缩量相对周围基体较小,不同位置处的最大温差达到最大值 185.2 ℃。


以上分析表明,叶片常规退火热处理升温与降温过程中,钛合金叶片叶根部位与周围基体存在较大温差,这极易导致钛合金叶片尤其是叶根部位在热处理过程中产生热应力分布不均匀的现象。
在后续服役过程中,叶片受力类似悬臂梁模型,空气压力在叶身上形成力矩,使叶身发生变形,叶片所受力矩从叶尖到叶榫逐渐增大,在加载初始阶段,叶身整体应力分布较为均匀,在叶根部位存在应力最大值,如图 12(a)所示,且叶根部位的应力在循环加载过程中不断增大,加载结束时叶根部位承载的应力达到最大值,叶身整体应力分布变得更加不均匀,如图12(b)所示。
上述仿真分析结果表明,在叶片成形及热处理阶段,成形应力不均以及温度场不均,均易导致叶片在叶根附近产生损伤缺陷,包括不均匀的应力分布,甚至是局部应力集中;而叶片服役阶段的仿真结果表明,叶片在服役过程中的最大承载点很可能出现在组织性能状态较差的叶根部位。叶根处存在内在损伤缺陷,与外载荷叠加时,使叶片在叶根部位更易产生疲劳裂纹,最终导致叶片发生疲劳破坏,如图5所示。
4、 电磁冲击对叶片疲劳性能影响机理分析
4.1 电磁脉冲能量对钛合金叶片材料微观作用机理
根据晶格动力学理论,可以将晶体内部单个晶粒及与之关联的微观缺陷(如晶界、相界、位错等)之间的关系视为简单的质量−弹簧系统。在此基础上,可将晶粒(弹性体)和微观缺陷(黏性体,具体包括晶界、相界、位错和杂质原子等)构建为二阶共振体系,如图13所示。
在外力作用下,该二阶共振体系满足以下平衡关系[35]:
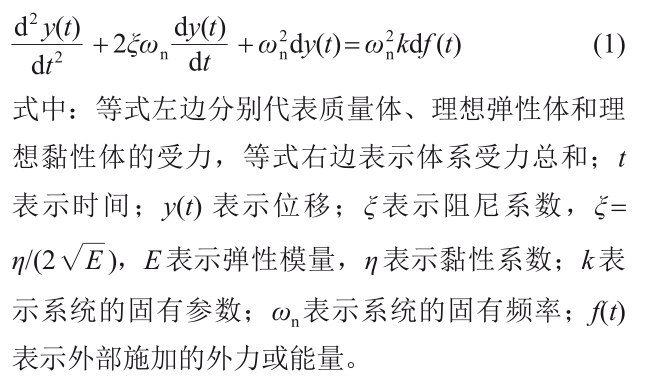
当一个周期性或准周期性的外力或能量,如电磁冲击过程中电磁脉冲能量作用于成品零件时,电子在电磁力的作用下会发生周期性的振荡。无电子散射时,电子的周期性振荡可视作原始驱动源,从而引起原子的振荡,进而导致合金中的晶粒和缺陷发生微振荡。如果条件合适,在成品零件中的某些微区,这种引起晶粒和缺陷发生微振荡的能量在没有能量耗散的情况下会被无限放大。经过拉普拉斯变换,二阶共振系统的传递函数H(s)如下[35]:
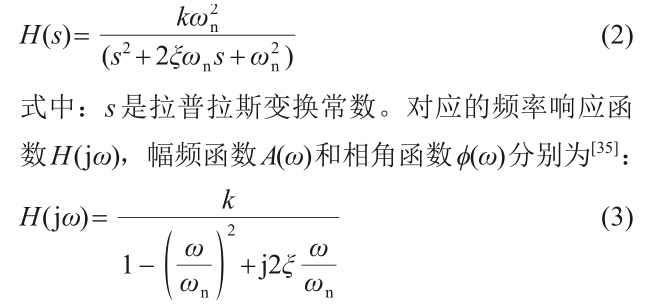
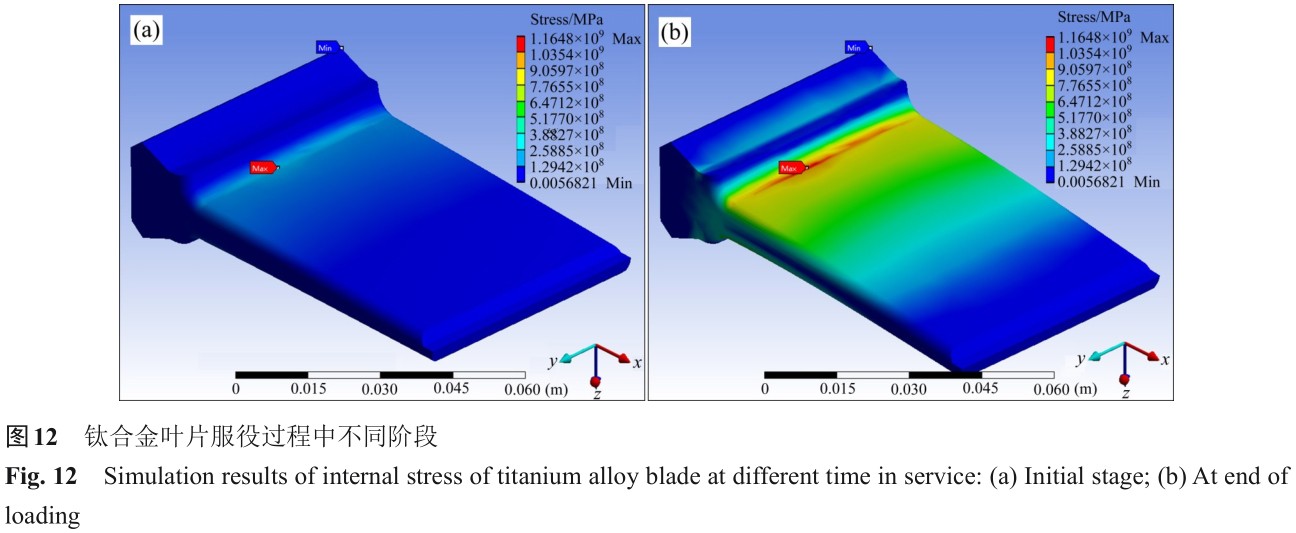
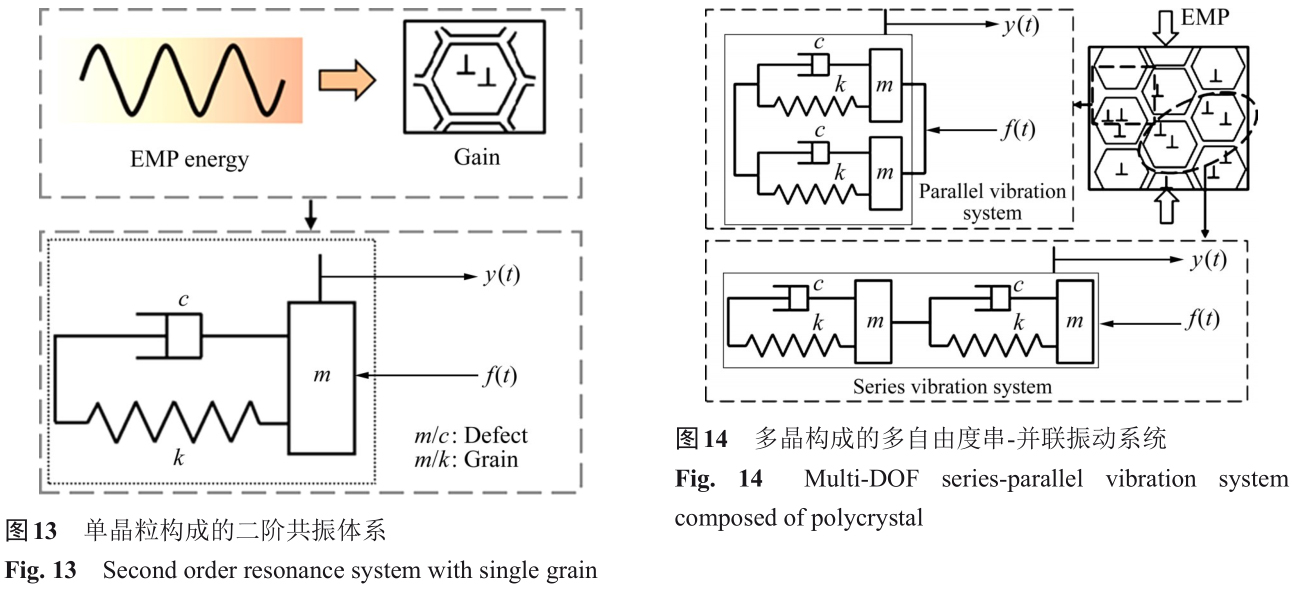
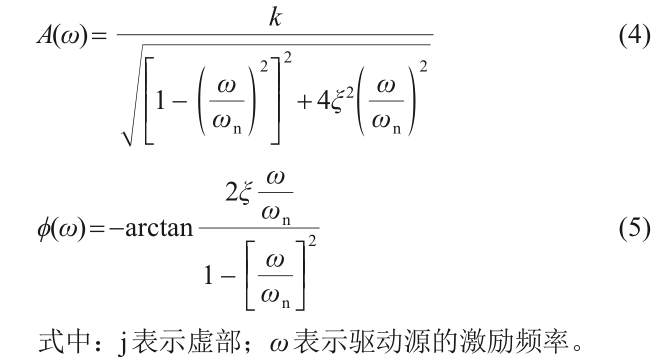
根据式(3)~(5),二阶共振系统这种能量放大效应取决于体系的固有频率ωn,外部激励频率ω和体系的阻尼系数ξ。当外部激励频率与固有频率的比值(ω/ωn )等于 1 时,发生共振,体系阻尼系数 ξ 越小,系统的振动程度越剧烈。
对于成品零件,从某种程度上来讲,实际晶体内部晶粒之间的关系可视为多自由度质量−弹簧系统的集合,如图 14 所示。且不同位置处晶粒的弹性和黏性性质并不一致,例如,合金中微织构区域的弹性和黏性性质(或应力状态)与其他区域明显不同。因此,实际晶体中可构建多个多自由度二阶共振体系,存在多个共振频率。
当电磁脉冲能量以振荡的形式作用在成品零件上时,考虑到合金中电磁场分布的不均匀性,不同位置处会产生不同的响应。在这个过程中,存在两种极端情况:1) 在外界激励条件下,当外界振动频率和该系统某共振频率一致时,发生共振,晶体内晶粒将发生剧烈振动;2) 晶粒不发生任何变化,例如,经过变形的合金存在特殊的微区域(微织构区域或应力集中区域),晶粒的振动通过连续振荡愈演愈烈,通过位错运动,从弹性变形演变为塑性变形,晶粒处于压缩或拉伸状态;最终,当这种振动超过了晶粒的屈服极限后,就会使晶粒发生屈服,甚至在缺少约束的表面局部微区(微米尺度)发生剧烈位移[35]。
大部分情况下,合金中不同位置处的响应介于上述两种极端情况之间,不同位置处的晶粒会发生不同程度的弹性或塑性变形,同时,不同位置处的晶体缺陷也会发生不同程度的重新排列。
4.2 电磁脉冲能量对钛合金叶片微观损伤缺陷的影响
叶片在成形制造及加工过程中,由于受到不均匀的温度场和应力场的影响,在一些局部微区易产生微织构,其产生的应力集中往往形成疲劳源[42],当微区应力集中超过强度极限时,则可能产生微观裂纹,甚至扩展形成大的孔洞。因此,成品叶片基体中,存在微观损伤(如夹渣夹杂、叠层、微裂纹及微织构等)和微观缺陷(如晶界、相界、位错、杂质原子等),从纳米到微米尺度不等。这些损伤缺陷无法避免,且其对叶片疲劳失效的影响不可忽视。
在控制焦耳热效应作用使叶片基体材料不发生传统热力学相变的条件下,电磁脉冲能量的微振荡效应在热激活作用下对钛合金叶片中不同位置处的损伤缺陷会产生不同程度的扰动,其中微观缺陷,如位错、杂质原子、空位等发生迁移并重新排列,相界、晶界结构重组,潜在的微观损伤,如微织构、微裂纹等被调整或修复,叶片整体建立新的应力场。最终,对叶片微观损伤缺陷可能会产生以下影响:1) 诱导原子、空位迁移,减少晶格结构畸变程度[18],改变晶格参数;2) 去除杂质原子,例如可减少氢原子含量[43],从而减缓或者避免服役过程中叶片失效[44];3) 激活位错迁移、增值[32]、堆积、纠缠及湮灭,调整残余应力分布[45−46],促进位错均匀分布,建立更稳定的应力场[47];4) 晶界发生迁移,晶粒发生轻微振荡并转动到更稳定的状态;5) 局部微区内的微裂纹通过塑性变形愈合[48−50],尤其是当焦耳热的作用适当参与其中时,在热力耦合作用下,效果更明显;6) 调整局部微织构的状态,从而减缓甚至抑制裂纹形核[51];7) 局部微区在电磁脉冲诱导的多种效应作用下发生非传统热力学相变[52];等等。
叶片材料金相组织中显著被影响区域虽仅为局部微区(微米尺度),对叶片基体材料力学性能可能影响不大,但对叶片基体材料组织性能的均匀性和稳定性影响较大,最终效果是,在无宏观塑性变形及无明显温升条件下,微观损伤被修复,微观缺陷被重组,同时,叶片整体残余应力得到有效调控(见图 6),最大应力数值及位置发生改变,改善局部应力集中,其综合作用有利于提高叶片疲劳性能(见图4),尤其是疲劳性能的一致性和稳定性[53]。
4.3 电磁冲击对叶片服役过程裂纹分布的影响
电磁冲击过程中,钛合金叶片试样表面最大温度控制在 60 ℃左右,而且,电磁冲击处理前后,钛合金叶片材料金相组织未发现可见变化,同时,叶片长度方向中部剖面显微硬度平均值随着电磁冲击峰值电流的增大而增加,增幅仅分别为 1.7% 和4.6%,但叶片长度方向中部剖面显微硬度沿叶身方向的分布产生了可见变化,如图 7 所示。这表明,电磁冲击处理对叶片基体金相组织无明显影响,但其不仅可以调控叶片表面残余应力(见图 6),还可调控叶片内部的残余应力分布(见图7)。
叶片服役时,假设施加在叶片表面的载荷为均匀分布的等压空气应力,针对本文所建叶片几何模型,叶身受力截面为变截面,沿叶片叶身长度方向纵截面厚度不一致,以叶片长度方向中部纵截面受力情况为例进行说明,其等效受力分析如图 15 所示。服役过程中,叶片长度方向中部纵截面等效受力(q)分布如图15(a1)所示,结合叶身受力截面积(s)大小 (见图15(a2)),计算得到叶片振动过程中的理论等效应力(σ)分布如图15(a3)所示。电磁冲击处理前,叶片根部材料内部可能存在锻造损伤,同时,经锻造和热处理后,该区域很可能形成局部应力集中,因此,服役时叶片内应力会与空气载荷叠加后的总的应力分布如图 15(b1)所示,可见,叶片根部应力最大,与有限元模拟结果相对应(见图 12)。
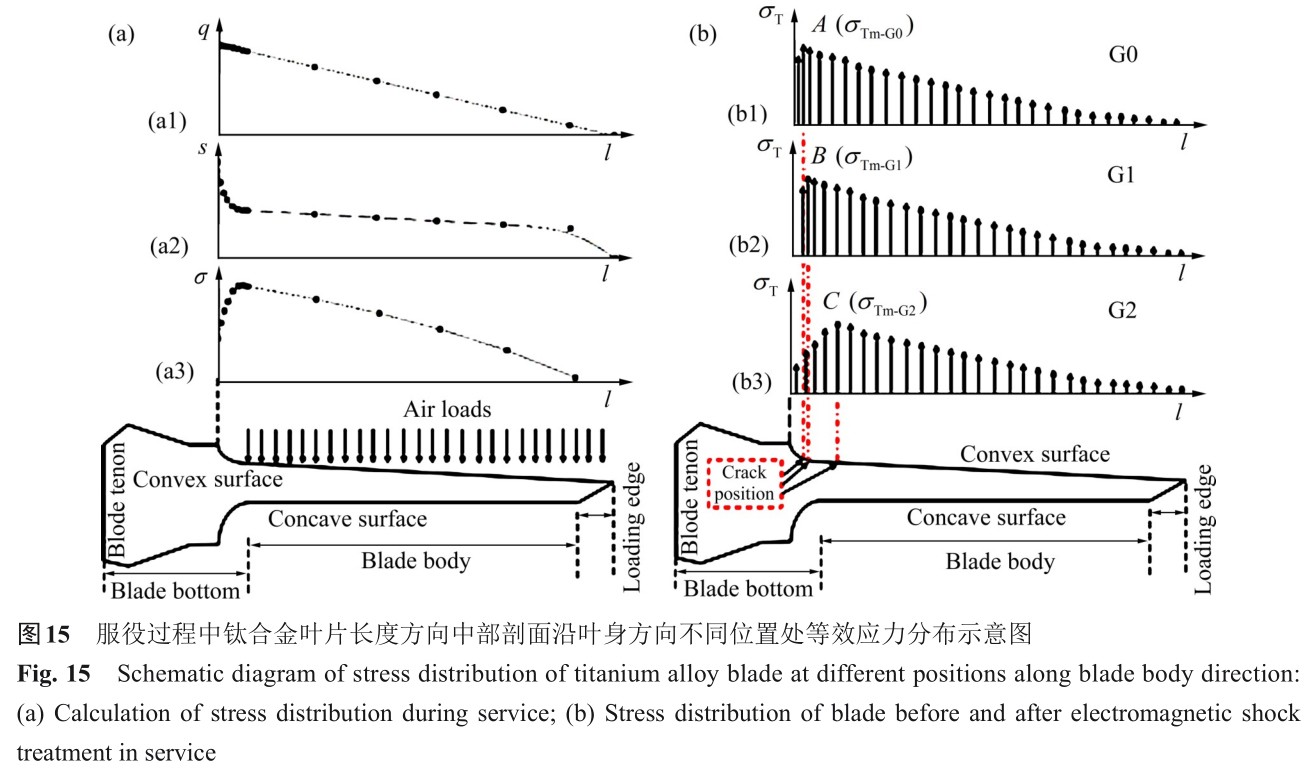
经电磁冲击处理后,随着电磁冲击电流密度由220 A/mm2增加至270 A/mm2,由图7叶片内部截面硬度分布变化可推测,叶片内部沿叶身方向残余应力最大处所在位置由叶根向叶身方向迁移,从位 置 A 分别转变为位置 B 和 C,且应力最大值σTm - G0>σTm - G1>σTm - G2(见图15(b)),从而导致叶片振动疲劳失效后疲劳裂纹失效位置从A分别变为B和C。
以上分析表明,电磁冲击处理不仅可以消减叶片材料内部的残余应力大小,还可调整叶片材料内部最大应力所在位置,进而影响叶片服役过程中疲劳失效裂纹位置(见图5)。
综上所述,电磁冲击过程中,电磁脉冲能量能够对叶片材料产生微振动效应,进而对材料微结构产生非线性激励作用,从而调整叶片局部微织构,愈合叶片中潜在的局部微裂纹等,调控叶片整体残余应力分布,改善叶片疲劳性能及其稳定性。
5 、结论
1) 电磁冲击处理可显著提高 TC11钛合金叶片的振动疲劳极限。当电磁冲击峰值电流密度由0 A/mm2、220 A/mm2增加到270 A/mm2时,叶片疲劳极限由492 MPa、528 MPa提升至672 MPa。
2)电磁冲击处理可调控TC11钛合金叶片表层残余应力分布及内部显微硬度分布。当电磁冲击的峰值电流密度由 0、220 A/mm2增加到 270 A/mm2时,叶片表层残余压应力逐渐增大;失效叶片剖面从叶榫端到叶尖端的显微硬度分布由高到低转变 为由低到高,且平均显微硬度由 302.8HV0.2、308HV0.2增加到316.8HV0.2。
3) 电磁冲击处理过程中,电磁脉冲能量能够对叶片材料产生微振动效应,进而对材料微结构产生非线性激励作用,从而调整叶片局部微织构,愈合叶片局部微裂纹,调控叶片整体残余应力分布。
4) 电磁冲击前后叶片的显微组织和力学性能未见明显变化,可推测,叶片电磁冲击后疲劳极限显著提高的主要原因有:一方面,在电磁脉冲能量作用下,叶片内部局部潜在微裂纹的愈合,以及微织构的调整均对疲劳性能稳定性和一致性的提升有促进作用;另一方面,电磁冲击调控了叶片整体残余应力分布,尤其是叶片根部残余应力的分布,使叶片根部的局部高应力区应力值降低,局部高应力区所在位置由叶片根部转移至叶身区域,有利于改善叶片疲劳性能。
REFERENCES
[1]LI Xiu-yan, LU Ke. Playing with defects in metals[J]. Nature Materials, 2017, 16(7): 700−701.
[2]LU Ke, LU Lei, SURESH S. Strengthening materials by engineering coherent internal boundaries at the nanoscale[J].Science, 2009, 324(5925): 349−352.
[3]VÖHRINGER O. Relaxation of residual stresses by annealing or mechanical treatment[J]. Residual Stresses,1987, 4: 367−396.
[4]HUANG Jie, ZHANG Kai-ming, JIA Yun-fei, et al. Effect of thermal annealing on the microstructure, mechanical properties and residual stress relaxation of pure titanium after deep rolling treatment[J]. Journal of Materials Science & Technology, 2019, 35(3): 409−417.
[5]CHIN K S, IDAPALAPATI S, ARDI D T. Thermal stress relaxation in shot peened and laser peened nickel-based superalloy[J]. Journal of Materials Science & Technology,2020, 59: 100−106.
[6]KWOFIE S. Plasticity model for simulation, description and evaluation of vibratory stress relief[J]. Materials Science and Engineering A, 2009, 516(1/2): 154−161.
[7]WANG Jia-sang, HSIEH Chih-chun, LIN Chi-ming, et al.The effect of residual stress relaxation by the vibratory stress relief technique on the textures of grains in AA 6061 aluminum alloy[J]. Materials Science and Engineering A,2014, 605: 98−107.
[8]廖 凯, 熊冠华, 朱家豪, 等 . 振动时效对 7075 铝合金薄壁构件应力松弛的影响与分析[J]. 振动与冲击, 2019, 38(1):265−270.
LIAO Kai, XIONG Guan-hua, ZHU Jia-hao, et al. Effects of vibratory stress relief on stress relaxation of 7075 Al alloy thin-walled components[J]. Journal of Vibration and Shock,2019, 38(1): 265−270.
[9]徐 野, 杨 蔚, 朱 平, 等 . 热时效对 A7N01 铝合金焊后残余应力及性能的影响[J]. 兵器材料科学与工程, 2015,38(4): 61−64.
XU Ye, YANG Wei, ZHU Ping, et al. Effect of heat ageing on residual stress and mechanical property of welded A7N01 aluminum alloy[J].Ordnance Material
Science and Engineering, 2015, 38(4): 61−64.
[10] 马永波, 崔腾飞, 潘一帆, 等 . 振动时效处理对 7055-T7751铝合金疲劳性能的影响[J]. 机械工程材料, 2019, 43(8):35−40.
MA Yong-bo, CUI Teng-fei, PAN Yi-fan, et al. Effect of vibratory stress relief treatment on fatigue property of 7055-T7751 aluminum alloy[J]. Materials for MechanicalEngineering, 2019, 43(8): 35−40.
[11] MILLER M K, BABU S S, SOKOLOV M A, et al. Effect of stress relief temperature and cooling rate on pressure vessel steel welds[J]. Materials Science and Engineering A, 2002,327(1): 76−79.
[12] BERGLUND D, ALBERG H, RUNNEMALM H. Simulation of welding and stress relief heat treatment of an aero engine component[J]. Finite Elements in Analysis and Design, 2003, 39(9): 865−881.
[13] ALBERG H, BERGLUND D. Comparison of plastic,viscoplastic, and creep models when modelling welding and stress relief heat treatment[J]. Computer Methods in Applied Mechanics and Engineering, 2003, 192(49/50): 5189−5208.
[14] BERMAN A. Extending the potential of evaporative cooling for heat-stress relief[J]. Journal of Dairy Science, 2006, 89(10):3817−3825.
[15] 沈华龙. 铝合金厚板振动时效工艺以及效果的研究[D]. 长沙: 中南大学, 2008: 6−7.
SHEN Hua-long. Study on vibration aging technology and effect of aluminum alloy thick plate[D]. Changsha: Central South University, 2008: 6−7.
[16] 郭俊康. 铝合金厚板振动时效的微屈服机理探讨与试验研究[D]. 长沙: 中南大学, 2010: 5−7.
GUO Jun-kang. Discussion and experimental study on micro yield mechanism of vibration aging of aluminum alloy thick plate[D]. Changsha: Central South University, 2010: 5−7.
[17] EDRY I, SHOIHET A, HAYUN S. On the effects of electric current intensity and pulse frequency on the solidified structure of pure aluminum subjected to pulse magneto-oscillation treatment[J]. Journal of Materials Processing Technology, 2021, 288: 116844.
[18] STEPANOV G V, BABUTSKII A I, CHIZHIK A V, et al. Pulse electric current effect on mechanical properties of titanium aluminide produced by the self-propagating high-temperature synthesis technique[J]. Strength of Materials,2012, 44(6): 636−644.
[19] 刘大海, 周文华, 李春峰 . U 形件磁脉冲辅助弯曲回弹控制 及 变 形 分 析 [J]. 中 国 有 色 金 属 学 报 , 2013, 23(11):3075−3082.
LIU Da-hai, ZHOU Wen-hua, LI Chun-feng. Springbackcontrol and deformation analysis for electromagnetically assisted bending of U-shaped parts[J]. The Chinese Journal of Nonferrous Metals, 2013, 23 (11): 3075−3082.
[20] SÁNCHEZ EGEA A J, GONZÁLEZ ROJAS H A,CELENTANO, D J, et al. Electroplasticity-assisted bottom bending process[J]. Journal of Materials Processing
Technology, 2014, 214(11): 2261−2267.
[21] MAL'TSEV I M. Electroplastic rolling of metals with a high-density current[J]. Russian Journal of Non-ferrous Metals,2008, 49(3): 175−180.
[22] LIU Y Z, ZHAN L H, MA Q Q, et al. Effects of alternating magnetic field aged on microstructure and mechanical properties of AA2219 aluminum alloy[J]. Journal of Alloys and Compounds, 2015, 647: 644−647.
[23] SONG Hui, WANG Zhong-jin. Grain refinement by means of phase transformation and recrystallization induced byelectropulsing[J]. Transactions of Nonferrous Metals Society of China, 2011, 21(S2): s353−s357.
[24] LIU Chang, XIE Le-chu, QIAN Dong-sheng, et al.Microstructure evolution and mechanical property response of TC11 titanium alloy under electroshock treatment[J]. Materials and Design, 2021, 198: 109322.
[25] SONG Xin-da, WANG Feng, QIAN Dong-sheng, et al.Tailoring the residual stress and mechanical properties by electroshocking treatment in cold rolled M50 steel[J].Materials Science and Engineering A, 2020, 780: 139171.
[26] KRAVCHENKO V. Y, Effect of directed electron beam on moving dislocations[J]. Russian Physics Journal,1967, 24: 1135−1142.
[27] ROSCHUPKIN A M, BATARONOV I L. Physical basis of the electroplastic deformation of metals[J]. Russian Physics Journal, 1996, 39(3): 230−236.
[28] PAUL S H, THOMAS K, Electromigration in metals[J].Reports on Progress in Physics, 1989, 52: 301−348.
[29] PRASAD S N, SINGH P N, SINGH V. Influence of pulsating magnetic field on softening behaviour of cold rolled AISI 4340 steel at room temperature[J]. Scripta
Materialia, 1996, 34(12): 1857−1860.
[30] ANDRE D, BURLET T, KÖRKEMEYER F, et al.Investigation of the electroplastic effect using nanoindentation[J]. Materials & Design, 2019, 183: 108153.
[31] ZHAO Shi-teng, ZHANG Ruo-peng, CHONG Yan, et al. Defect reconfiguration in a Ti-Al alloy via electroplasticity[J].Nature Materials, 2021, 20: 468−472.
[32] YAN Jia-wei, LI Wei, LIU Hai-ting, et al. Reversion of sub-boundaries into dense dislocations in aluminum by electric pulsing treatment[J]. Scripta Materialia, 2019, 167: 86−90.
[33] CAI Zhi-peng, ZHAO Hai-yan, JIAN Lin, et al. Plastic deformation caused by pulsed magnetic treatment of mid-carbon steel[J]. Materials Science and Engineering A, 2007,458(1/2): 262−267.
[34] XIE Le-chun, GUO Hao-jie, SONG Yan-li, Effects of electroshock treatment on microstructure evolution and texture distribution of near-β titanium alloy manufactured bydirected energy deposition[J]. Materials Characterization,2020, 161: 110137.
[35] SUN Qian, HUA Lin. Micro texture of titanium alloys excited nonlinearly by electromagnetic pulse[J]. Scripta Materialia, 2021, 200: 113828.
[36] VENKATESH B D, CHEN D L, BHOLE S D. Effect of heat treatment on mechanical properties of Ti-6Al-4V ELI alloy[J]. Materials Science and Engineering A, 2009, 506:117−124.
[37] LI Yang-yang, MA Shu-yuan, LIU Chang-meng, et al.Microstructure and mechanical properties of Ti-6.5Al-3.5Mo-1.5Zr-0.3Si alloy fabricated by arc additive manufacturingwith post heat treatment[J]. Key Engineering Materials, 2018, 789: 161−169.
[38] 戴全春, 宋燕利, 华 林, 等. 航空发动机钛合金叶片残余应力喷丸−电磁场复合调控技术[J]. 武汉理工大学学报,2016, 38(8): 13−17.
DAI Quan-chun, SONG Yan-li, HUA Lin, et al. Residual stress shot peening electromagnetic field composite control technology for aeroengine titanium alloy blades [J]. Journalof Wuhan University of Technology, 2016, 38(8): 13−17.
[39] 李 娜, 尹喜刚, 刘 静, 等 . 锻造仿真与热模拟技术在航空发动机叶片精密锻造中的应用[J]. 航空制造技术, 2018,61(15): 59−62, 68.
LI Na, YIN Xi-gang, LIU Jing, et al. New technology and application of numerical control machining for aero-engine blade[J]. Aeronautical Manufacturing Technology, 2018,61(15): 59−62, 68.
[40] YANG Qi, ZHOU Wen-long, ZHONG Yi-ning, et al. Effectof shot-peening on the fretting wear and crack initiation behavior of Ti-6Al-4V dovetail joint specimens[J].International Journal of Fatigue, 2018, 107: 83−95.
[41] 陈思觉 . 钛合金叶片的真空退火工艺试验[J]. 材料工程,1994(3): 31−33.
CHEN Si-jue. Vacuum annealing process test of titanium alloy blade[J]. Journal of Materials Engineering, 1994(3): 31−33.
[42] BIAVANT K L, POMMIER S, PRIOUL C. Local texture and fatigue crack initiation in a Ti-6Al-4V titanium[J]. Fatigue & Fracture of Engineering Materials & Structures. 2001, 25:527−545.
[43] 戚运莲, 洪 权, 卢亚锋, 等. 氢对钛合金组织及加工性能的影响[J]. 钛工业进展, 2010, 27(6): 10−15.
QI Yun-lian, HONG Quan, LU Ya-feng, et al. Effects of hydrogen on process and microstructure and properties of titanium alloys[J]. Titanium Industry Progress, 2010, 27(6):10−15.
[44] XIANG Si-qi, MA Rui, ZHANG Xin-fang. Removing hydrogen in solid metal using electric current pulse[J].Journal of Alloys and Compounds, 2020, 845: 156083.
[45] CAI Zhi-peng, HUANG Xin-quan. Residual stress reduction by combined treatment of pulsed magnetic field and pulsed current[J]. Materials Science and Engineering A. 2011, 528:6287−6292.
[46] WU Wen-lin, SONG Yan-li, ZHOU Pu, et al. Mechanical properties improvement of pre-deformed Al-Zn-Mg-Cu alloys by electroshocking treatment based on the non-equilibrium scattering of electron-dislocation[J]. Journal of Alloys and Compounds, 2020, 861: 157987.
[47] TAKEMOTO R, NAGATA M, MIZUBAYASHI H. Effects of passing electric current on the elastic property of amorphous Cu 50 Zr 50 and Cu 50 Ti 50[J]. Acta Materialia,1996, 44(7): 2787−2795.
[48] WANG Feng, QIAN Dong-sheng, HUA Lin, et al. Voidshealing and carbide refinement of cold rolled M50 bearing steel by electropulsing treatment[J]. Scientific Reports, 2019,9(1): 11315.
[49] HOSOI A, NAGAHAMA T, JU Y. Fatigue crack healing by a controlled high density electric current field[J]. Materials Science and Engineering A, 2012, 533: 38−42.
[50] 周亦胄, 罗 申, 贲昊玺, 等 . 在脉冲电流作用下钢中裂纹的愈合[J]. 材料研究学报, 2013, 17(2): 169−172.
ZHOU Yi-zhou,LUOShen,BENHao-xi,et al. Experimental study on crack healing in steel using electric current pulse technique[J]. Chinese Journal of Materials and
Research, 2013, 17(2): 169−172.
[51] XU Yi-lun, JOSEPH S, KARAMCHED P, et al. Predicting dwell fatigue life in titanium alloys using modelling and experiment[J]. Nature Communications, 2020, 11(1): 5868.
[52] 张 伟, 隋曼龄, 周亦胄, 等 . 高密度电脉冲下材料微观结构的演变[J]. 金属学报, 2013, 39(10): 1009−1018.
ZHANG Wei, SUI Man-ling, ZHOU Yi-zhou, et al.Electropulsing-induced evolution of microstructures in materials[J]. Acta Metallurgica Sinica, 2013, 39(10):
1009−1018.
[53] SHAO Quan, WANG Gang, WANG Hai-dou, et al.Improvement in uniformity of alloy steel by pulsed magnetic field treatment[J]. Materials Science & Engineering A, 2021(799): 140143.
相关链接