1、钛合金的特点、应用与分类
航空制造业通常是衡量一个国家制造水平高低的标准,是一个国家先进制造水平和技术实力的集中体现。自上个世纪五十年代以来,航空航天工业在迅猛发展。为了满足先进尖端设备能够在极端环境下的正常运行,先进材料也在探索发展,因此金属钛和钛合金应运而生。在 1910年,美国科学家 “亨特”使用“钠法”制造出金属钛。随后的几十年发展里,对先进的制作钛工艺也在摸索前进。但直到 1948 年,飞跃性的金属钛制备技术—“镁法制钛”才被卢森堡科学家提出。从此时开始,世界各国才开始大规模的使用和研究金属钛和钛合金。
在现有的地球矿产资源储备中,钛元素在金属材料储备排序中排在第四位,仅次于铁(Fe)、铝(Al)和镁(Mg)。相比较与铁、铝和镁等元素,钛和钛合金具有优秀的使用性能,其中典型的材料属性有:
(1)比强度高(强度/密度),钛合金的比强度约在 200-300。相比较于合金钢,钛合金的强度区间为 980-1300MPa,略小于合金钢的 1250-1600MPa,但是由于钛合金(4.5g/cm3)的密度约有合金钢(7.9 g/cm3)的一半,相同体积下钛合金质量更轻,性能更好。
(2)热强度和低温性能好,目前低温钛合金可以在-253°C 环境下工作,并保持良好的使用性能,高温钛合金可以在 350°C—650°C 环境下服役使用。相比较其他材料,钛合金在极端温度下具有优秀耐受性。
(3)抗腐蚀性能优异,钛元素在低于 550°C 的空气中,易于空气中的氧元素发生化学反应,钛合金表面会形成一种均匀的、致密的薄膜。这个薄膜可以有效地阻碍钛元素与强酸、强碱和复杂环境下的其他元素发生化学反应,维持钛合金的稳定性。钛合金的抗腐蚀性均优于常规不锈钢等材料。
无磁、超导、弹性模量小和硬度较高等也是钛合金的优秀特性。
从上述可以看到,钛合金是一种性能优异,存储丰富且研究还未成熟的年轻金属。
结合这些优点,从上 20 世纪 50 年代起,世界各国在先进工业领域就开始给予钛合金足够多的重视,加大了对新型钛合金的制备和钛合金的研究应用。
目前在常温状态下,根据钛合金的退火组织可将钛合金主要分为以下 3 类:
(1)α 钛合金,α 钛合金是钛元素与硼、铝等元素相容后得到的。国内的 α 钛合金简称为 TA,其退火后微观结构呈密排六方体结构。α 钛合金的特点为高温强度好,常温强度低,抗氧化性和抗腐蚀性优秀。
(2)β 钛合金,钛元素中加入一定量的铬、钼、钒等元素就可形成 β 钛合金,β 钛合金在国内牌号为 TB,其退火后微观结构呈体心立方体结构,并可进行热处理强化。
(3)α+β 钛合金,也称两相钛合金。国内的 α+β 钛合金牌号为 TC,该材料结合了 α钛合金和β钛合金的优点,可以进行热处理,但焊接性能稍差于α钛合金,综合性能好。
常用各类代表性的钛合金如下表 1 所示。
在上述部分内容中讨论了钛合金棒、钛合金管等钛合金的性能和分类,作为年轻的太空金属,钛合金自发现开始,就逐渐成为重要的航空材料。在航空应用方面,钛合金主要集中在以下两个部分。
(1)钛合金在飞机上的应用
美国、俄罗斯和中国等先进国家均在军事领域和民用领域对钛合金的应用进行了研究。表 1.2 为各国飞机上钛合金的使用占比。图 1.1 为不同类型钛合金在 F-22 猛禽战斗机上的使用情况。结合表 1.2 和图 1.1 可以看出,先进飞机上钛合金的使用比例均很高,钛合金的占比和飞机的性能成正比,同时也应用在更多的飞机零部件上。在 21 世纪,衡量一个飞机是否先进,一个重要指标即为钛合金的使用占比。我国钛合金工业起步较晚,在钛合金的应用和应用领域上仍有很大的进展。
(2)钛合金在航空发动机上的使用
航空发动机是飞机的心脏部位,航空发动机运转环境是高温、高压的极端情况。发动机的大部分关键零部件在运作过程中要承受极高的压力和表面高温(如:叶片)。因此在选择使用材料时,要求材料能够在 550°C-700°C 时,保持良好的高温强度、高温蠕变性和稳定的化学性。在传统的材料中,铝合金耐高温性差,并且钢和其合金密度高,重量大,因此均不是最合适的材料选择。同时衡量一个航空发动机是否优秀的重要指标既是推重比,在 20 世纪早期,飞机的推重比均在 5 以下,但随着工业的发展,现阶段飞机的推重比可达到 10 左右。随着金属钛的出现和钛合金优秀性能的开发,钛合金逐渐成为了航空发动机材料的最佳选择。目前钛合金在航空发动机上主要应用部件有:燃烧室、发动机叶片、压气机盘和防火壁等,钛合金在航空发动机上的使用比例也在升高,在我国早期 1978 年生产的涡喷-13 系列发动机上,钛合金的使用比例仅为 13%。在后来 2002年生产的涡喷-14(昆仑)发动机上,使用比例为 15%。美国普惠公司在 1970 年生产的第三代 F100 发动机,其钛合金使用比例为 25%。而在 1994 年生产的第四代 F119 发动机上,钛合金的使用比例为 40%。表 1.3 为各国航空发动机在不同温度下钛合金的应用选材情况。从表 1.3 可以看到钛合金可以满足航空发动机不同温度区间下的使用需求。随着工业的发展和航空产品的生产迭代,钛合金在飞机和航空发动机中使用占比愈发提高。在同时期我国航空用钛合金使用比例远远低于美国,在材料应用与技术扩展上,仍有很大的进步空间。
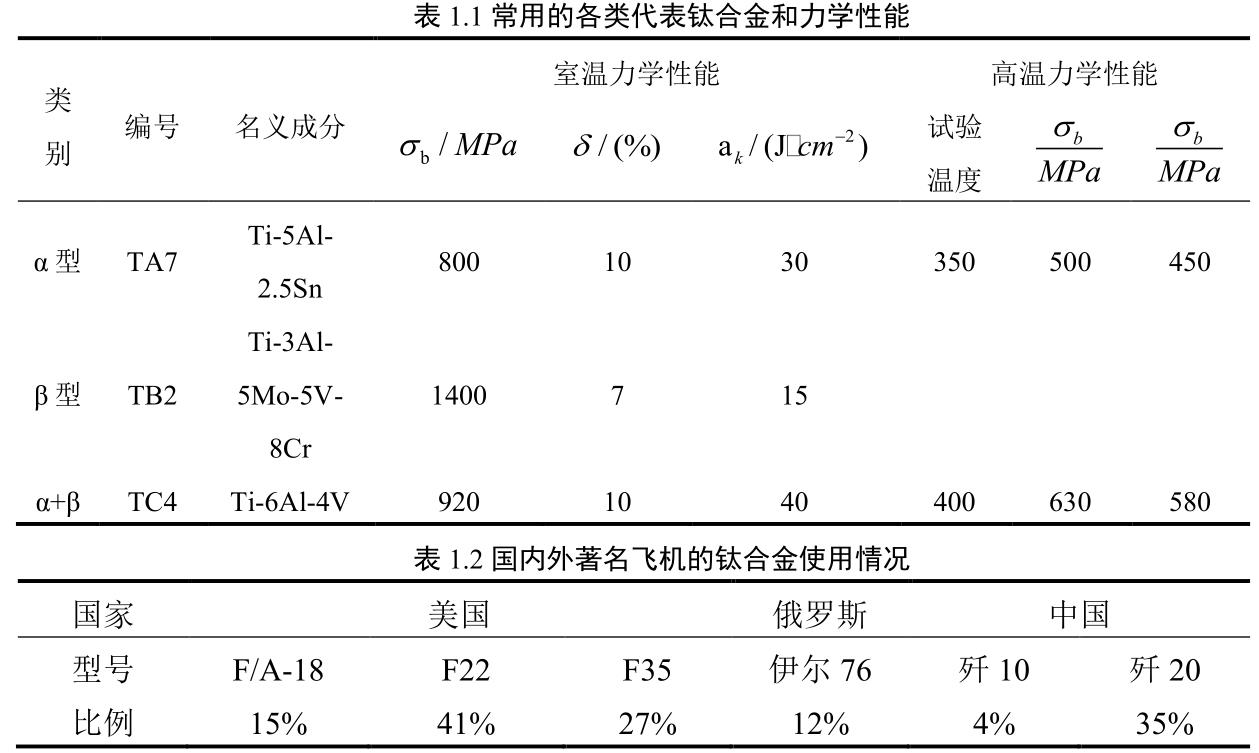
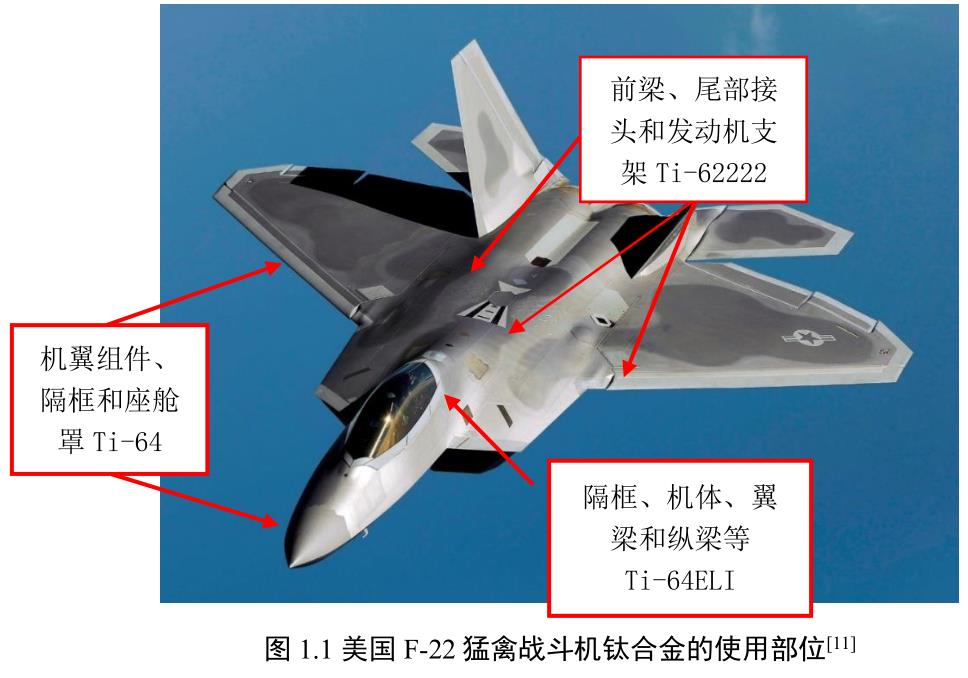
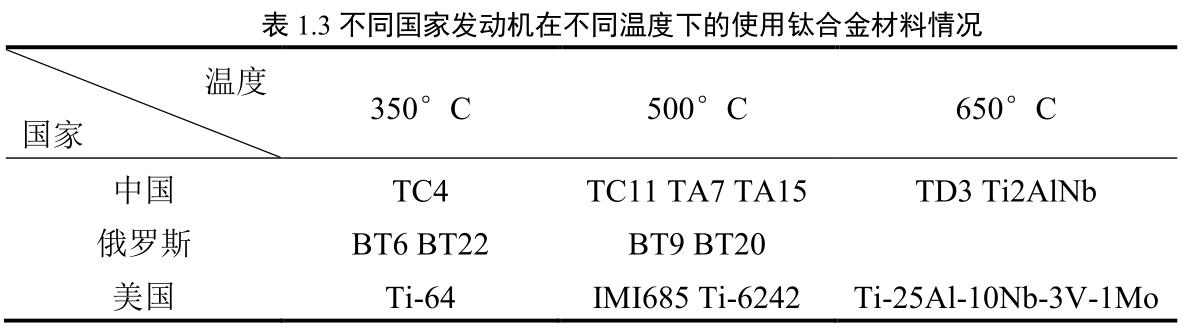
2、 钛合金加工存在的问题
在 1.1.1 节中讨论可知,钛合金是性能优异的材料,十分适合应用于极端环境。但同时钛合金也属于难加工材料,根据相对加工性准则,钛合金的相对加工性仅有普通 45 钢的 20%-40%。相比较于传统金属切削加工方面,钛合金具有不同于传统金属(钢、铝合金和镁合金)的加工特点。加工钛合金主要有以下特点。
(1)导热性差、热传导率低
钛合金的导热系数仅为λ=15.24 W/(m·K),约为铁的 20%,远低于铝的导热系数。
切削加工是一个稳态的、长期的过程。钛合金导热系数差,热传导率低,加工时就会导致切削热聚集在刀具刀尖的一部分小区域面积上。切削时刀尖此部分承受了切削热总量的 80%-90%,这些集中的切削热加剧了刀具的磨损,促进了刀具与工件表面之间的元素扩散和金属的高温相变,图 1.2 为刀具因切削热过大导致的磨损。
(2)弹性模量小、摩擦系数大。
钛合金的弹性模量小,TC4 和 TC11 的弹性模量分别为 110GPa 和 123GPa,约为钢材料的一半。材料的弹性模量小容易发生弹性变形,而钛合金不仅弹性模量小,同时屈服比大。在切削过程中,第三变形区的工件表面会发生材料回弹,回弹后的材料会与刀具的后刀面相接触,增大刀具后刀面的磨损。对比传统材料切削,在切削钛合金时,刀具与材料接触面的摩擦系数更大,需要克服摩擦所做的功就越多,从而刀具-切屑接触面的温度升高,接触面易于发生粘结磨损,材料剥落形成月牙湾。
(3)刀具与切屑接触长度短,切削力大
相比较于钢材料的切削,切削钛合金时产生的主切削力小于切削钢材产生的,主切削力约占钢材的 2/3-3/4。但是对比两者切削时的刀具-切屑接触长度发现,钛合金的接触面积
很小,切削力主要集中在前刀面和刀尖的一小面积上,切削力大刀尖材料易剥落发生崩刃现象,从而刀具失效。图 1.3 是切削力过大导致的刀具破坏失效。
(4)钛合金硬度较低、化学活性高
钛合金的化学性质是很活泼的,在高温和高压的切削环境中易与空气中的氧元素、氢元素等发生化学反应,从而在加工过程中形成表面硬化层。提高了钛合金的硬度,阻碍刀具的切削,使得钛合金的塑性降低。切削过程中化学性能活泼,刀具和工件间元素易发生置换和转移,使得刀具表面材料发生改变,影响切削稳定性,促进了刀具磨损。
(5)切屑问题
在加工钛合金的过程中,钛合金的切屑呈絮状,类似于棉花,缠绕在刀尖和工件附近。在切削加工时需要往刀尖加工部位注入冷却液,冷却液可以及时带走切削过程的产热。结合钛合金的切削特点和实际加工过程,不难可以为实际加工做出指导性建议,即切削液应尽可能的喷在刀尖加工区域,同时在发生切屑缠绕时,应及时的清理切屑,以免因切削热量无法及时散出而导致刀具破坏。图 1.4 时切削钛合金产生的切屑。
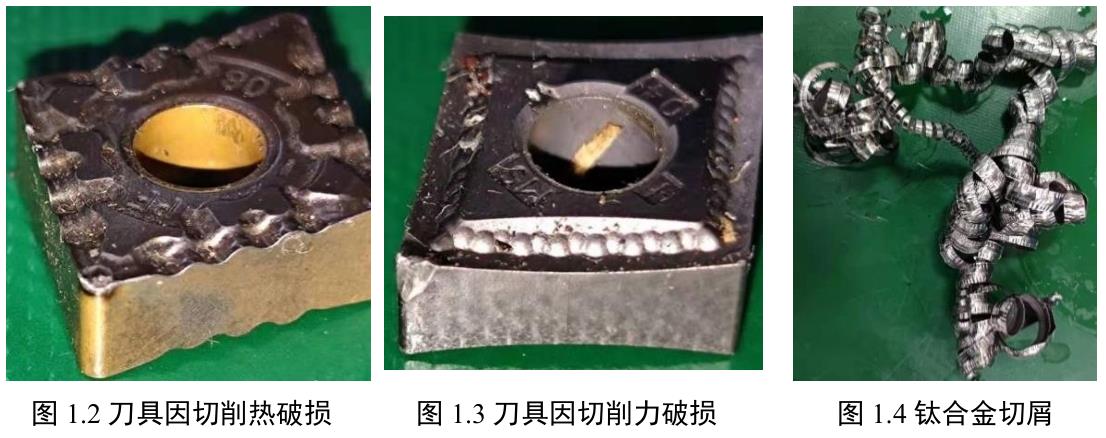
3、常用钛合金加工刀具
加工钛合金的刀具主要分为以下几种。
(1)高速钢刀具
高速钢刀具是指含有较多钨(W)、铬(Cr)、钼(Mo)和钒(V)等材料元素的合金刀具,一般高速钢刀具具有硬度较低、红硬性较差和热导率低的特点。只有部分高速钢刀具牌号可以用来进行钛合金切削,但整体应用面窄,适用于切削的有:高钒高速钢、钴高速钢和铝高速钢等。对高速钢刀具组成成分功能分析,含 Co的高速钢刀具使用寿命较长于其他刀具,主要原因为钴元素(Co)的添加可以增加刀具的硬度、耐磨性和导热性。尽管钴元素可以提高高速钢刀具的切削性能,但也难以保证长时间切削的加工精度和加工稳定性。在高温高压的切削过程中,高速钢刀具中的 W、V 等元素易于钛合金材料中的元素发生粘结—扩散磨损。因此结合高速钢刀具的切削性能和使用成本,高速钢刀具通常应用于低速加工和粗加工钛合金阶段。
(2)硬质合金刀具
硬质合金刀具是使用粉末冶金工艺将金属碳化物和粘结剂烧结制成。硬质合金刀具耐用性好、加工性能稳定,是目前主流的加工钛合金的刀具材料。在粉末冶金工艺中,晶粒尺寸影响着硬质合金刀具的使用性能。常规的硬质合金刀具,其晶粒尺寸在几μm之间。对于精密切削用的硬质合金刀具其晶粒尺寸可达 1μm 左右。烧结过程中减小晶粒尺寸,可以提高晶粒间的相互结合力,晶粒粘结更敦实,整体性能更均匀,耐磨性和硬度均优于粗晶粒制备的刀具。按照组成成分可将硬质合金刀具主要分为以下三类:钨钴类(YG类)、钨钛钴类(YT类)和添加稀有金属碳化物类。根据钛合金的切削特点,常用钨钴类硬质合金刀具来加工钛合金,不常用钨钛钴类硬质合金刀具。这是由于在钨钛钴类硬质合金刀具中存有一定量的钛元素(TiC),在高温高压的切削条件下,刀具和工件中的钛元素易发生粘结—扩散磨损,使得刀具过早的产生磨损失效,并且钨钛钴类硬质合金相比较于钨钴类硬质合金材料较脆,在切削过程中,刀具容易发生刀尖崩坏等非正常磨损失效。钨钴类硬质合金刀具的抗弯强度、韧性和硬度均优于钨钛钴类,刀具能够承受一定量的冲击和振动,可减少在切削过程中刀具的非正常磨损破坏,延长服役时间,降低刀具使用成本。钨钴类刀具导热性好,有利于降低切削温度,钴含量愈高,则刀具韧性愈好,适用于精密加工。常用的钨钴类硬质合金刀具牌号有:YG6X、YG8、YG3 和 YG3X。
(3)超硬刀具材料
超硬刀具是新兴的应用于钛合金管、钛合金板等钛合金加工的刀具材料,在钛合金的加工领域有着良好的应用前景。超硬刀具材料种类主要包括:立方氮化硼刀具(CBN)、聚晶立方氮化硼刀具(PCBN)和金刚石刀具。目前的我国超硬刀具材料主要应用于民用领域和非金属切削领域,其中金刚石刀具主要用于非铁材料的加工。金刚石主要分为:天然单晶金刚石、人造聚晶金刚石和金刚石烧结体这三种。国外学者[17]已经使用聚晶金刚石刀具(PCD)高速切削钛合金,优化了切削参数,得出了最优组。超硬刀具材料的硬度高,热导率高散热性能好,能够有效的应用于钛合金的精加工和高速加工方面。但是受约束于超硬刀具材料的应用成本,使得超硬刀具材料无法大范地在车间生产过程中使用。英国学者Farhad Nabhani[18]对比分析了 PCD 刀具、CBN 刀具和 KC850 硬质合金刀具在切削钛合金时的刀具寿命问题,实验表明 PCD 刀具的使用寿命是 CBN 刀具的两倍以上,是 KC850刀具的三倍以上,相比之下 PCD 刀具是适合钛合金加工的。
总而言之,在选择刀具进行钛合金材料切削时,主要以硬质合金刀具材料为主,部分高速钢刀具可以用来进行毛坯加工和粗加工。在不考虑刀具使用成本的前提下,超硬刀具材料更适合应用于精密和超精密加工。表 1.4 为各类刀具材料的力学性能。
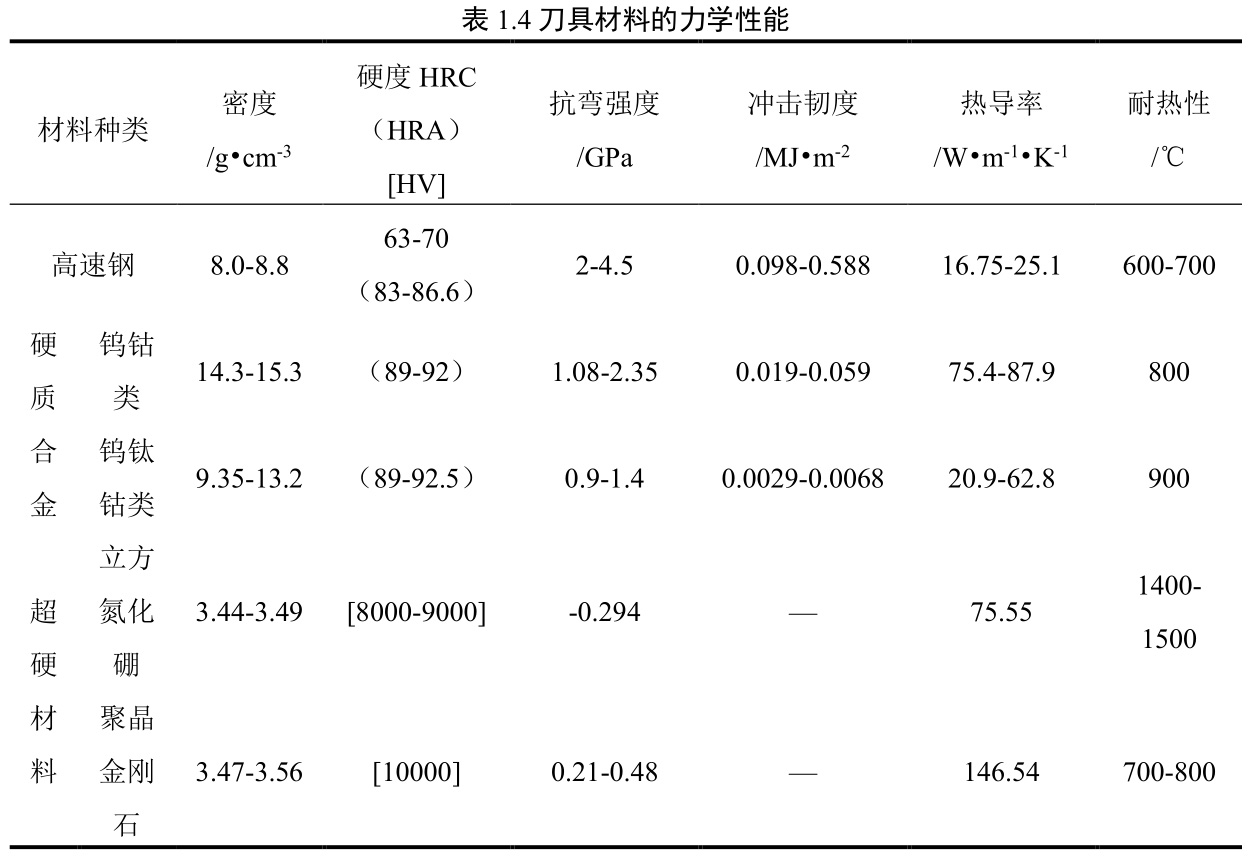
相关链接