钛合金管是航空航天、海洋船舶、石油化工和石油勘探中大型设备常用的关键机械零件[1,2],该类零件的深孔一般是通过深孔钻镗孔工艺或斜轧穿孔及轧制获得。钻镗孔工艺直接利用深孔钻对钛合金棒材进行钻削,材料的利用率不足50%,对于某些大孔径的薄壁钛合金管,其利用率更低,不足10%,因此造成大孔径钛合金管的加工成本很高[3,4]。斜轧穿孔及轧制是目前无缝管生产中应用较广的工艺之一,采用该工艺时钛合金消耗小,但是其设备复杂、周期长、成品率低,且该工艺仅应用于低强度钛合金的加工,而对于高强度钛合金管的轧制工艺,目前尚处于研究阶段[5-7]。

深孔套料钻削工艺因断屑和排屑困难、加工状况处在半封闭状态下不便观察等因素成为深孔加工方面的难题[8,9],对于钛合金材料加工,更是受到其工艺、刚度、强度、切削刀具的磨损、导向块磨损和排屑难等诸多因素影响[10-12],使钛合金深孔套料的加工难度增加,最终出现如排屑出口堵屑、入钻不稳定、套料过程振动现象严重、崩刀现象等问题[13,14],使得钛合金深孔套料技术成为目前一个重要的难题。
为了解决上述问题,以降低工艺成本,节约原材料和减少机床的功率消耗。本文以大孔径钛合金管的加工为背景,设计了大孔径钛合金管深孔套料钻削工艺。
针对大孔径钛合金管套料钻削过程中存在的这些问题,从工艺的角度出发,提出了一定的解决方法,并进行了大孔径钛合金深孔套料钻削试验,试验结果表明:采用以环形切削方式在实体材料上进行大孔径钛合金管深孔套料钻削工艺,能节约大量的钛合金原材料,并且能得到比较高的加工质量。
该工艺的发展为大孔径钛合金管的生产提供了新的工艺途径。与传统的钻镗孔工艺相比,大孔径钛合金管深孔套料钻削工艺具有工艺简单、材料利用率高、刀具成本低和机床磨损小等优点。
1、深孔套料加工系统
根据钛合金材料的切削性能特点和工件结构,为了更顺畅的排屑,钛合金深孔套料加工系统采用外排屑深孔套料钻削系统。该系统主要由深孔钻镗床、深孔套料钻和冷却排屑系统三大部分组成,如图1所示。该系统运动方式为工件旋转、钻杆进给。切削液通过钻杆的尾部进入钻杆内部,经钻杆内壁和工件的间隙进入套料钻的头部进行冷却润滑,并将形成的切屑从钻杆外壁和工件的间隙中排出,所获得的钛合金管和芯棒如图2所示。
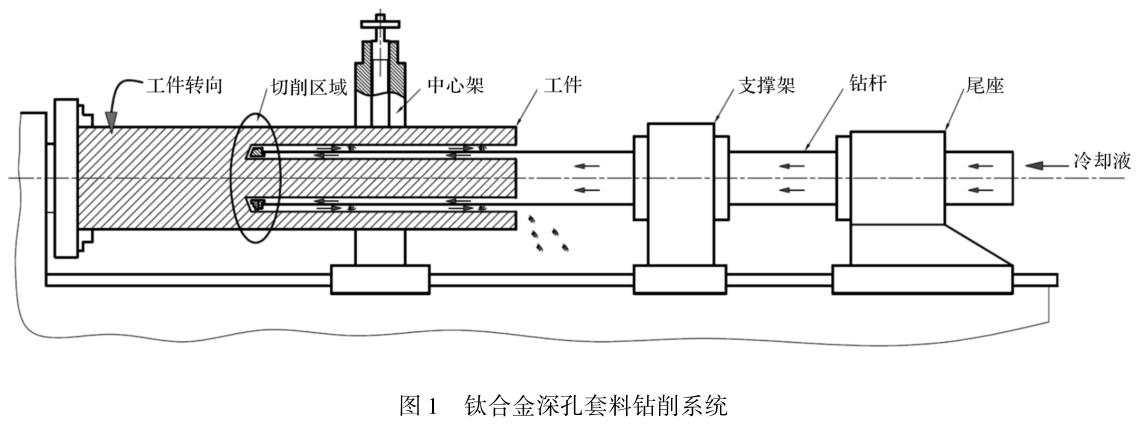
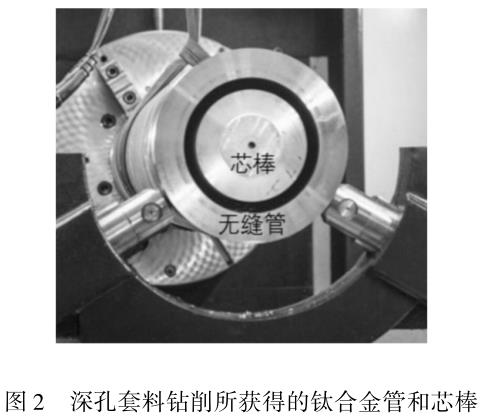
2、钛合金深孔套料关键技术
2.1.1深孔套料钻刀齿材料
钛合金材料的切削加工性能比较差,切削加工时切削速度比较低,在进行切削加工时,因其切屑呈锯齿状而造成了刀具切削力呈周期性变化,且刀具受到的切削冲击力比较大[15,16],因此,钛合金材料套料钻削时,宜选择强度高、抗冲击韧性较好的YG8硬质合金作为深孔套料钻的刀齿材料。YG8硬质合金抗弯强度比较高,且抗冲击性能和抗振性能都比较好,而其耐磨性能和允许的切削速度却比较低[17,18]。
2.1.2 深孔套料钻的结构及几何参数
深孔套料钻的结构如图3所示。对于钛合金材料,采用单齿外排屑深孔套料钻比较合适,多齿的深孔套料钻会产生比单齿深孔套料钻更大的振动,且多齿深孔套料钻的刀齿中要加入必要的搭接量势必要增大切削力,从而间接的增大了切削功率,提高了对机床的要求。
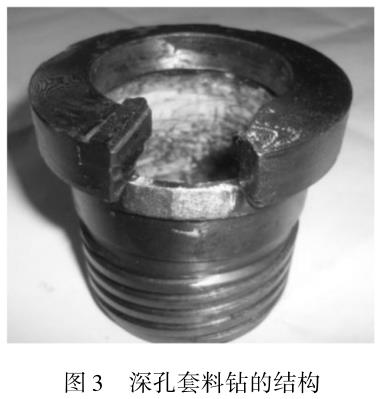
由于钛合金比强度和热强度高、切削变形系数和弹性模量小等特点[19,20],宜采用小前角、大后角以及较大的主偏角,使切削刃锋利耐磨,减小切屑变形。因此选取前角γ0为7°,后角α0为12°,主偏角kr为80°,刃倾角λs为0°。
根据钛合金材料特性,断屑槽结构选用圆弧型,其参数为:断屑台的宽度Wn为2.5~3.8mm,断屑台深度Hn取为0.5~1mm,圆弧半径Rn一般取为0.5~0.8mm。
为了实现很好的断屑,刀片采用了轴向阶梯分屑方式,在满足要求孔径的前提下,尽可能增大芯棒直径,以便节约材料,但为了更好的断屑和排屑,采用的单齿刀片为4级阶梯式刀片,切削刃总宽度为15mm,由外到内每齿宽度分别为3mm、4mm、4mm、4mm,分屑齿的结构如图4所示。
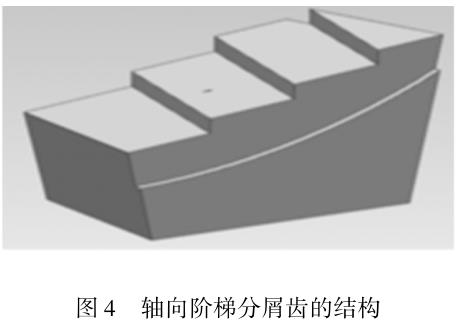
2.2 钛合金深孔套料排屑效果
对钛合金工件材料进行外排屑深孔套料加工时,由于钻削用量、刀具结构、切削液流量的不同而出现了不同的切屑形态。当切削速度在14.7~27.0mm/min之间,进给量处于f=0.10~0.15mm/r之间时,排屑和钻削过程非常稳定,切屑能很好的自动断屑,能实现长时间的套料加工。
当切削液的流量加大时,不仅能提高加工系统的刚性,还能使切屑自动断屑的周期变小,长屑变为短屑,但不同的切削液流量对套料钻的分屑效果影响不是很明显。因此,在对钛合金材料进行深孔套料加工时,应加大油路通道的截面面积,加大切削液的流量,使切屑在大流量的切削液作用下能较好的进行断屑和排屑,使钻削过程更加平稳。
深孔套料钻削的排屑过程主要是由高压切削液将切屑强制带出,切削液从钻杆的末端输入,到达切削部位带走切屑,再从钻杆的外侧将切屑带出,如图5所示。随着孔的深度的增加,切削液沿程阻力损失和切屑排出的路线就会增加,如果切削液压力小于或者等于切屑沿途的阻力,就导致带状切屑缠绕现象出现,使套料切削过程产生振动、崩刀、打刀,导致套料切削过程无法正常进行。通常情况下,采用加大切削液压力和流量,强制将切屑从切削区带走,以减小套料过程中切屑缠绕问题而产生的振动。
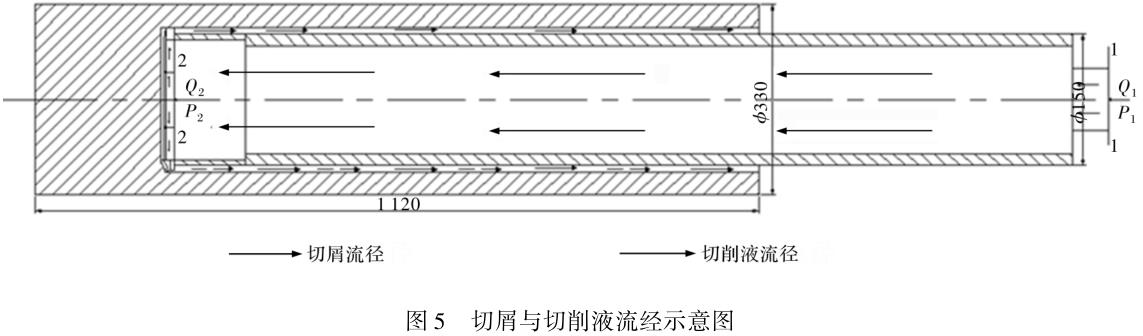
2.3 钻杆的强度及刚度
在深孔套料加工过程中,采用工件转动、刀具直线进给的加工方式。在钻杆向前移动、刀具与工件之间产生挤压的过程中,钻杆的前端部会受到工件向后的反作用力,反作用力的大小对于钻杆是否产生屈服具有一定的影响。因此,为了保证钻杆在加工过程中不因强度不够而影响加工,钻杆的最大工作压力不得超过40Cr材料的许用压力,及要求钻杆的强度条件为
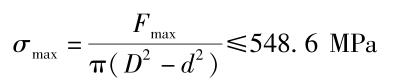
在工件的转动过程中,工件也会对钻杆的端部产生反向的扭矩,为了使钻杆在加工过程中克服此扭矩而产生的屈服失效,因此必须使杆内最大的扭转切应力不得超过40Cr材料的扭转许用应力,既满足钻杆的扭转强度条件为
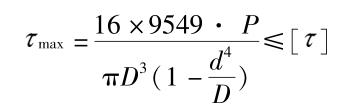
在加工过程中,转速过大时会使得扭转角过大,进而会引起强烈的振动,由于振动可导致打刀崩刀现象,因此需要对钻杆扭转变形做一定的限制,即满足钻杆的扭转刚度条件
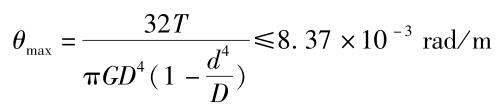
3、钛合金深孔套料钻削加工
3.1 加工条件及工艺参数
钛合金深孔套料采用外排屑深孔加工系统,试样为TC4棒料,尺寸为230mm×1200mm,如图6(a)所示。深孔套料钻直径为115mm,进给量为f=0.17mm/r、f=0.19mm/r、f=0.20mm/r、f=0.22mm/r,转速为110r/min、145r/min,切削液流量Q=125L/min、Q=250L/m,切削液压力2.5MPa。深孔套料加工过程如
图6b所示。
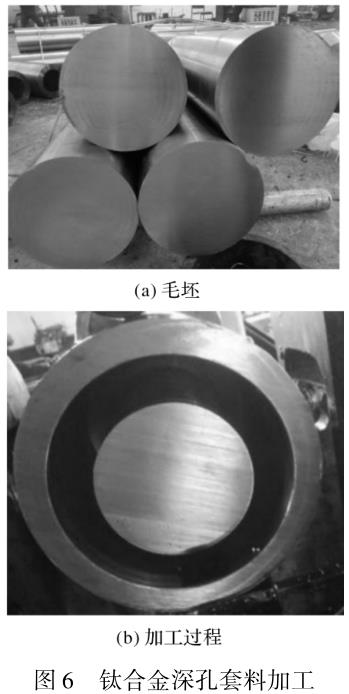
3.2 加工结果及分析
钛合金深孔套料加工结果如图7所示。该试件所有尺寸均达到设计要求。钛合金管孔壁和芯棒的尺寸精度均可达IT8,表面的粗糙度可达3.2μm。
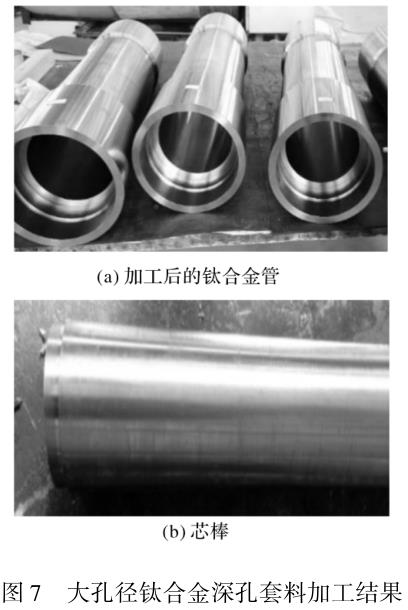
不同工艺参数组合下所获得的深孔套料钻削过程如表1所示。在钛合金深孔套料过程中,当转速一定时,随着进给量的增大,轴向钻削力和扭矩增大。当转速为110r/min、进给量为0.2r/min、切削液压力2.5MPa、切削液流量250L/min时,深孔套料钻削过程中没有发生堵屑现象,刀具出现轻微的钝化,如图8a所示。但在速大于110r/min、进给量大于0.20mm/r时,发生堵屑现象,并且靠近芯棒的一侧发生崩刀,如图8b所示。
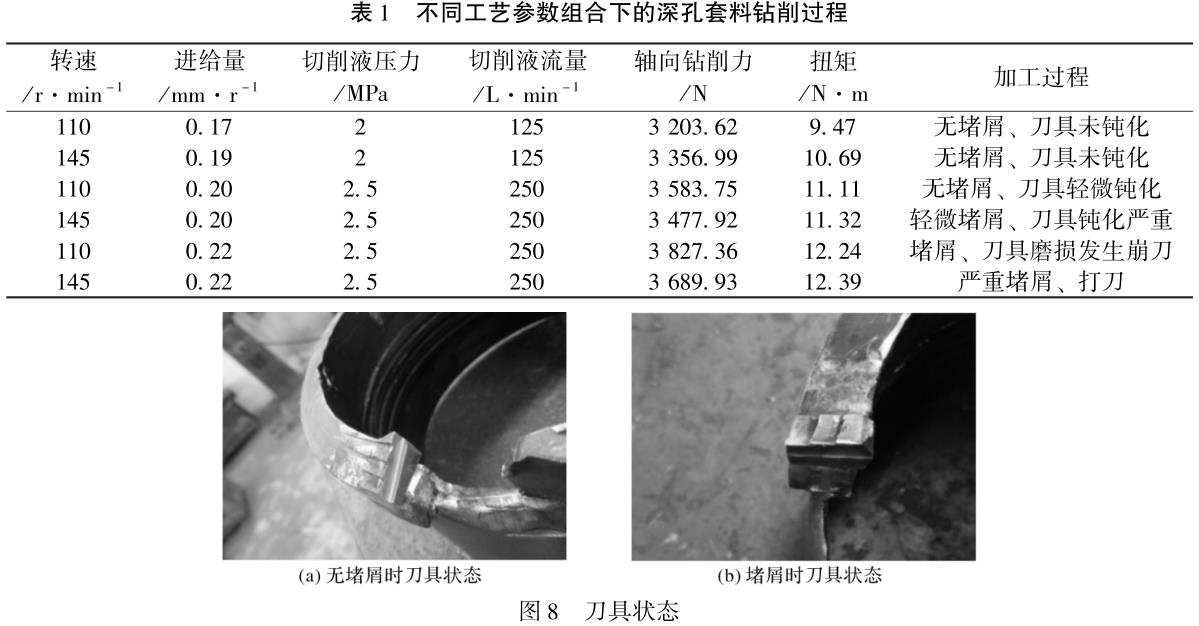
当进给量处于0.19mm/r和0.20mm/r之间时,切屑能实现自动分屑,其切屑形态如图9a所示,当转速为110r/min、切削液压力为2.5MPa、切削液流量为250L/min时,可实现顺利排屑,且钻削过程相对稳定,实现长时间的深孔套料加工。当进给量大于0.22mm/r时,切屑形态为挤裂状切屑,如图9b,套料过程中出现剧烈的振动,刀具磨损严重,容易造成套料钻头出现崩刃现象。
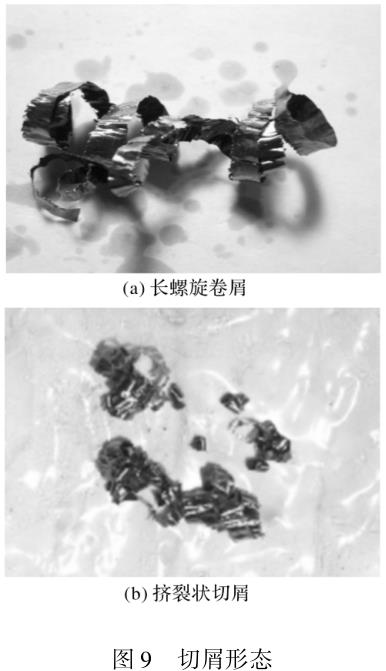
4、结论
通过对TC4钛合金工件进行批量深孔套料加工,可得出如下结论:
(1)套料加工的轴向力和扭矩要比深孔钻小,降低了对深孔钻削机床的功率要求,因而比其它深孔钻削方式更经济。
(2)套料钻几何参数采用γ0=7°,α0=12°,kr=80°,λs=0°,转速n=110r/min、进给量f=0.2mm/r、切削液压力P=2.5MPa、流量Q=250L/min时,钛合金深孔套料钻削过程比较平稳,切屑形态比较好。
(3)钛合金深孔套料加工所形成的切屑形态随着钻削用量、刀具结构、切削液流量以及钛合金材料种类的不同而不同,其中进给量对切屑形态影响最大。
(4)在孔径一定的条件下随着钻削长度的增加,切削液的沿程压力损失较大,为了切屑的有效排出,必须适当的增加切削液的压力和流量。在实际加工中,由于冷却润滑系统的密封性以及油泵功率的限制,通常采取增加流量Q,来提高加工时的排屑效果。
参考文献:
[1]房永强,余泽利,白新房,等.TA18钛合金管收缩应变比的测量不确定度评定[J].塑性工程学报,2021,28(12):230-236.
[2]蔡国帅,朱宝辉,陈胜川,等.冷轧和退火对TC4钛合金管组织和性能的影响[J].热加工工艺,2018,47(21):86-88.
[3]刘战锋,谢健康.TC4钛合金深孔(钻削)套料加工系统及其刀具研究[J].机床与液压,2019,47(15):114-118.
[4]冯亚洲,黄帅澎,刘雁蜀,等.TA15钛合金深孔钻削试验研究[J].制造技术与机床,2022,(02):39-42.
[5]庞玉华,何威威,刘东,等.TC4钛合金锥形辊斜轧穿孔曼内斯曼效应[J].塑性工程学报,2020,27(03):109-114.
[6]于浩,黄华贵,郑加丽,等.无缝钢管斜轧穿孔顶头表面缺陷非接触在线检测方法[J].中国机械工程,2021:1-8.
[7]张浩泽,余堃,钟海,等.铸坯斜轧穿孔制备大口径TA31钛合金无缝管材[J].兵器材料科学与工程,2022:1-7.
[8]LiuZ,ZhengW,ZhuH.ResearchonDrillingProcessofDeepHoleTrepanningforTitaniumAlloy(TC4)[J].DEStechTransactionsonComputerSci-enceandEngineering,2017.
[9]柴辉.短电弧套料加工电极头和电加工参数的研究[D].西安石油大学,2019.
[10]薛虎,李亮.切削液油压对深孔枪钻加工Ti6Al4V钛合金的影响研究[J].工具技术,2020,54(12):60-64.
[11]王宇.机夹式深孔钻头钻削TC4钛合金试验及刀具失效研究[D].西安:西安石油大学,2021.
[12]秦声,密思佩,明伟伟,等.钛合金深孔钻削温度测量及加工表面质量研究[J].机械设计与制造,2021,(07):155-157+162.
[13]刘战锋,韩晓兰.典型难加工材料深孔加工技术[M].北京:科学出报社,2020.
[14]许晓达,李全昆,郁红波.多芯管套料工艺改进[J].船海工程,2021,50(02):46-49.
[15]LuZ,ZhangD,ZhangX,etal.Effectsofhigh-pres-surecoolantoncuttingperformanceofhigh-speedultra-sonicvibrationcuttingtitaniumalloy[J].JournalofMateralsProcessingTechnology,2020,279:116584.
[16]张俊杰,刘英想,胡王杰,等.TC4钛合金纵弯超声振动铣削装置及其加工性能研究[J].航空制造技术,2022,65(08):14-21.
[17]原瑞泽,闫献国,陈峙,等.深冷处理对YG8硬质合金/42CrMo钢钎焊接头残余应力的影响[J].金属热处理,2021,46(10):204-208.
[18]梁伟印,梁国星,董黎君,等.YG8硬质合金表面激光熔覆WC/TIC/Co涂层的组织及性能[J].金属热处理,2021,46(12):168-174.
[19]王瑶,李永刚,李文辉,等.深冷处理对TC4钛合金滚磨光整加工性能的影响[J].稀有金属,2021,45(11):1289-1298.
[20]王欣,罗学昆,宇波,等.航空航天用钛合金表面工程技术研究进展[J].航空制造技术,2022,65(04):14-24.
相关链接