1、引言
钛合金因其优越的材料性能(比强度高、耐腐蚀、热强性好等),被越来越多地应用在航海、航天航空等设备的关键零部件上。同时,钛合金具有导热系数小、弹性模量小、回弹量大等特性,使其磨削加工性差,加工质量难以得到保证,加工效率低[1,2]。针对钛合金平面磨削加工中的问题,国内外学者开展了许多有意义的研究。韩野等[3]对金刚石砂轮磨削钛合金时的主要工艺影响因素(如进给速度、磨抛深度等)进行了试验分析,优选出更合适的工艺参数。刘伟等[4]以TC4钛合金为研究对象进行高速外圆磨削实验,分析了外圆磨削工艺参数对工件表面完整性的影响规律,结果表明,表面质量随着砂轮线速度提高而提高;随着工件转速提高,表面划痕更加明显;随着磨削深度增加,出现表面烧伤现象,并且磨削深度对表面完整性的影响程度最大。NaskarA.等[5]研究了磨削进给量对TC4钛合金表面完整性的影响,结果表明,随着进给量增加,其表面残余压应力及表面粗糙度增加。ChenY.G.等[6]对钛合金进行了磨削试验,结果表明,砂轮线速度增加时,表面粗糙度先降低后略有增加;表面粗糙度值随磨削深度的增加而增大,工作台进给速度对磨削表面形貌影响较小;在高速磨削中,表面显微硬度随着砂轮线速度增加而急剧增加。肖鹏[7]对超高速磨削下TC4表面完整性进行了研究分析,结果同样表明,磨削工艺参数对磨削表面质量有着显著影响。因此,在磨削加工钛合金时,选择合理的砂轮参数和磨削用量是获得较好表面质量的关键[8]。
本文以TC4钛合金为研究对象,在乳化液条件下采用金刚石砂轮对TC4钛合金进行平面磨削试验,对比分析在不同粒度和磨削用量下的磨削表面粗糙度、显微硬度、微观组织以及表面残余应力的影响规律,优选出更适用于金刚石砂轮磨削钛合金的工艺参数。
2、试验条件及方案
2.1试验条件
试验用机床为改造的JASU/H-1900T卧式镗铣加工中心,最高转速为6000r/min,最大进给速度为4000mm/min。磨削砂轮安装在卧式主轴上,试验分别采用粒度为80,120和150的树脂结合剂金刚石砂轮,其规格为350mm×30mm×75mm。工件材料为退火态TC4钛合金,试件尺寸为40mm×20mm×20mm,化学成分如表1所示。
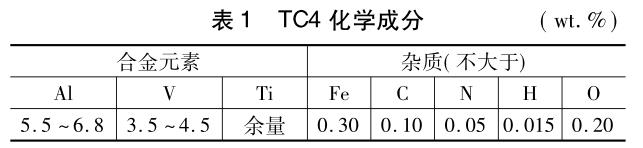
试验采用KISTLER9129A压电测力仪采集磨削力信号(见图1),用于测量工件所受的切向磨削力FX和法向磨削力FZ。试验后采用MahrS3P测量仪测量工件相对于砂轮在轴向进给方向的工件表面粗糙度,采用PULSTECμ-X360X射线残余应力分析仪测量砂轮磨削方向和垂直于砂轮磨削方向的工件表面残余应力,采用VHX-600三维光学显微镜对工件表面形貌和表面层微观组织检测,并采用乳化液冷却润滑。
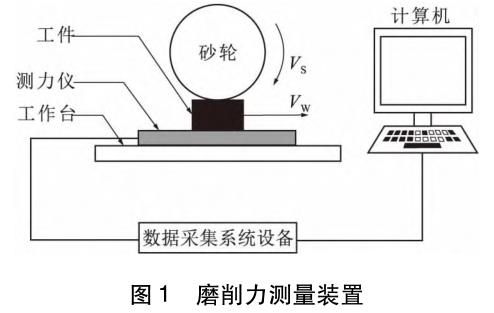
2.2试验方案
试验采用逆磨削方式,分析砂轮材料和磨削用量对TC4钛合金磨削力、磨削表面质量、磨削表面残余应力状态和钛合金形貌的影响规律,探寻适合TC4钛合金磨削加工的砂轮材料及磨削工艺参数范围,其参数设置见表2。
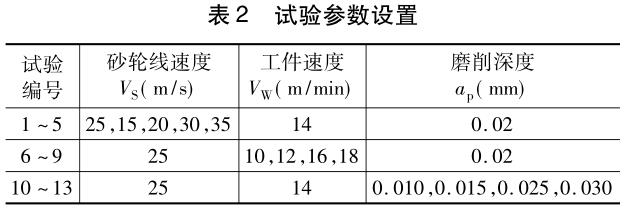
3、结果分析与讨论
3.1磨削表面粗糙度
图2a为表面粗糙度随砂轮线速度的变化情况,随着砂轮线速度的增大,磨削表面粗糙度呈下降趋势。这主要是因为随着砂轮线速度的增大,单位时间里参与磨削的磨粒数随之增加,工件塑性变形隆起增大使表面粗糙度值降低。实际加工中,在主轴功率和砂轮转速允许的情况下,应尽量选择半径较大的砂轮和较大的砂轮转速,以增大砂轮线速度,获得较好的表面粗糙度。图2b为表面粗糙度随工件速度的变化趋势。
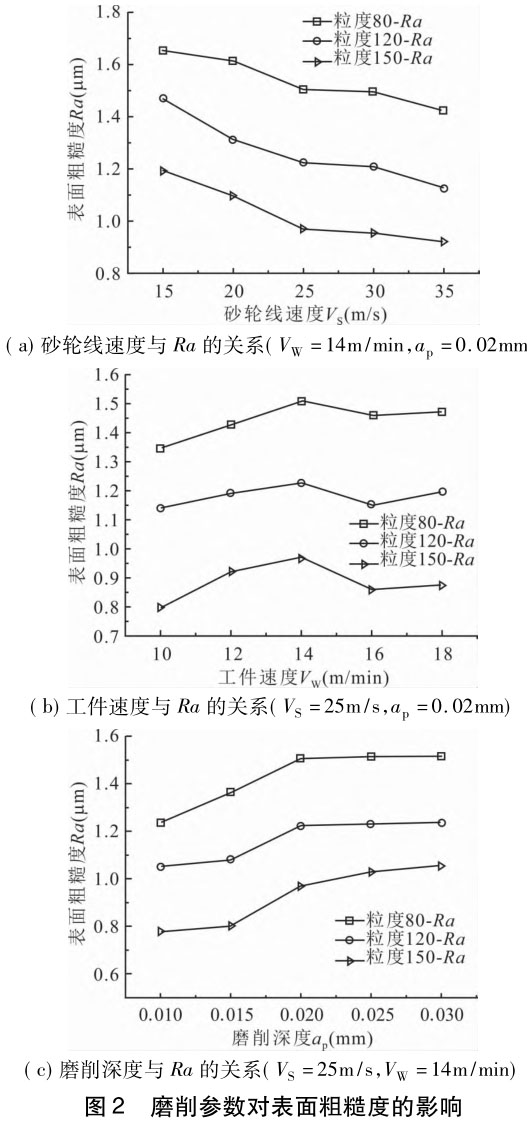
当砂轮线速度和磨削深度不变时,随着工件速度的增大,磨削表面粗糙度会有所增大并逐渐趋于稳定值,因此要想获得较低的表面粗糙度,需选择较低的工件速度进行加工。综合考虑加工效率等因素,工件速度也应尽量低于18m/min。
图2c为表面粗糙度随磨削深度变化的趋势。当砂轮线速度和工件速度不变时,随着磨削深度的增大,磨削表面粗糙度呈上升趋势。因此采用较小的磨削深度可以获得较高的表面质量。粗加工时采用较大的磨削深度,获得较高的材料去除率并提高加工效率;精加工尽量采用较小的磨削深度,获得较高的表面加工质量以提高加工精度。粗加工时,磨削深度并非越大越好,要根据砂轮粒度和性能选择合适的磨削深度,磨削深度过大会加速砂轮磨损,降低砂轮寿命,反而降低加工效率。
综上可知,砂轮粒度号越大,砂轮粒度越细,磨削表面粗糙度就越小。因此,采用较细粒度的砂轮加工可以获得较光滑的加工表面。加工中,粗加工时宜采用较粗粒度的砂轮,以获得较高的材料去除率,提高加工效率;精加工尽量采用较细粒度的砂轮,以获得较好的表面加工质量,提高加工精度。
3.2显微硬度分析
采用HXS-1000TAC显微硬度仪测量已加工表面显微硬度,选择维氏硬度单位,每组试验参数测量三个点,取三次测量结果平均值。图3a为工件表面显微硬度随砂轮线速度变化的趋势。120粒度的金刚石砂轮在乳化液条件下磨削TC4钛合金,当工件速度和磨削深度不变时,随着砂轮线速度的增加,工件表面显微硬度减小且逐渐趋缓;80粒度和150粒度的金刚石砂轮在乳化液条件下磨削TC4钛合金,工件表面显微硬度随砂轮线速度的增加并无明显变化。
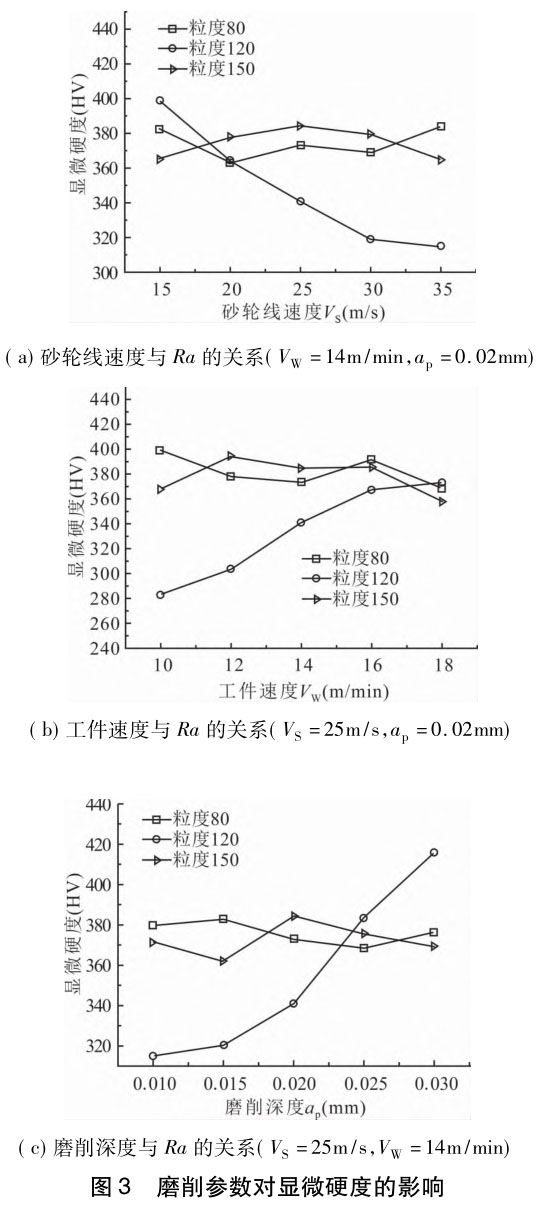
图3b为工件表面显微硬度随砂轮线速度变化的趋势。当砂轮线速度和磨削深度不变,120粒度的金刚石砂轮在乳化液条件下磨削TC4钛合金时,随着工件线速度的增加,工件表面显微硬度增大且增大趋势减缓;80粒度和150粒度的金刚石砂轮在乳化液条件下磨削TC4钛合金时,工件表面显微硬度随着工件速度的增加并无明显变化。
图3c为工件表面显微硬度随砂轮线速度变化的趋势。当砂轮线速度和工件速度不变,120粒度的金刚石砂轮在乳化液条件下磨削TC4钛合金时,随着磨削深度的增加,工件表面显微硬度增大且增大趋势加快;80粒度和150粒度的金刚石砂轮在乳化液条件下磨削TC4钛合金时,工件表面显微硬度随着磨削深度的增加并无明显变化。
综上,随着砂轮线速度提高,工件表面显微硬度减小;随着工件速度提高,工件表面显微硬度增大;随着磨削深度的提高,工件表面显微硬度增大。磨削深度对工件表面显微硬度的影响最大,砂轮线速度次之,工件速度影响最不明显。
3.3表面层微观组织分析
采用VHX-600三维光学显微镜检测工件表面层微观组织。将磨削参数分别设定为砂轮线速度VS=25m/s,工件速度VW=14m/min,磨削深度ap=0.02mm,金刚石砂轮在乳化液条件下磨削TC4钛合金。从图4可以看出,150粒度砂轮磨削工件表面质量最好,120粒度砂轮磨削工件表面质量次之,80粒度砂轮磨削工件表面质量最差。
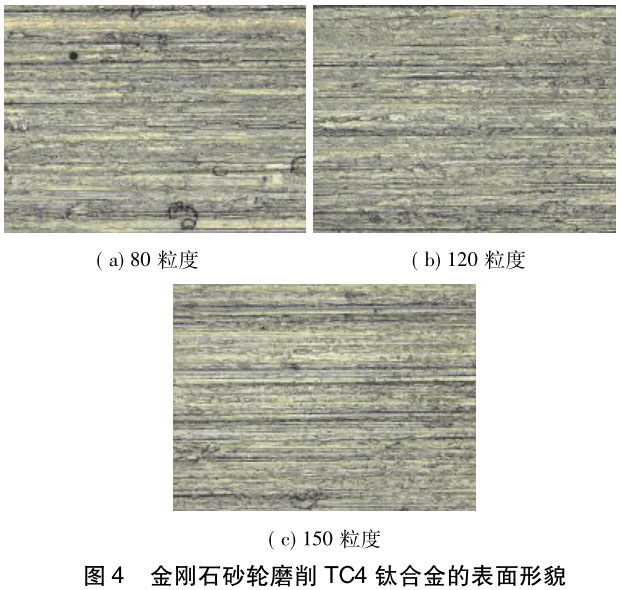
3.4磨削表面残余应力分析
以粒度为80的金刚石砂轮在乳化液条件下磨削钛合金为分析对象。图5a为表面残余应力随砂轮线速度变化的趋势。当工件速度和磨削深度不变时,随着砂轮线速度的增加,磨削热量增加,热应力增大,表面残余应力也会相应增大。因为砂轮线速度提高,单颗磨粒的平均未变形切屑厚度减小,塑性变形深度相应减小,相同单位时间内参与磨削的磨粒数增多。图5b为表面残余应力随工件速度变化的趋势。当砂轮线速度和磨削深度不变时,随着工件速度的增加,虽然磨粒未变形,但磨屑厚度增大,发热量增大,砂轮与工件的接触时间缩短,即热源在工件表面的移动速度增大,表面残余应力降低。
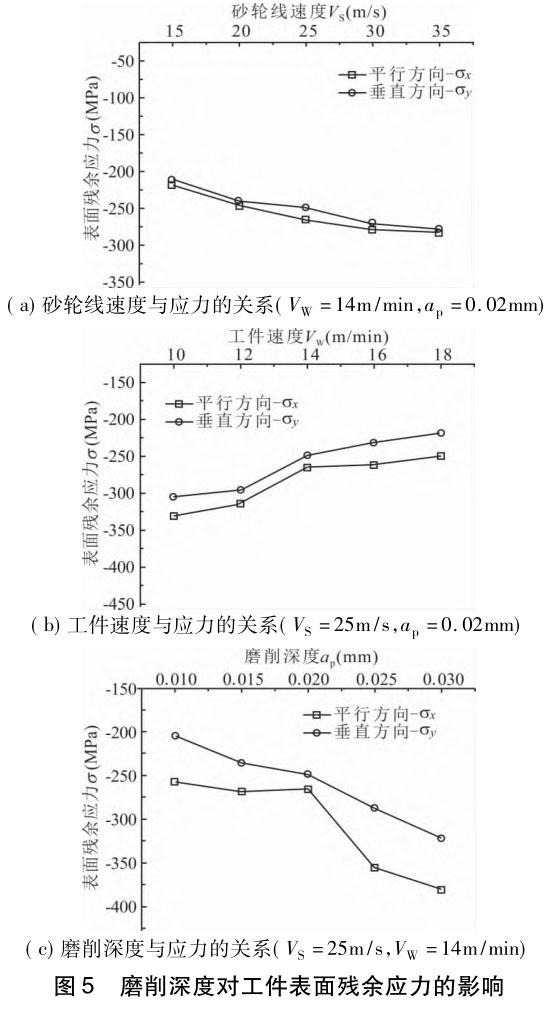
图5c为表面残余应力随磨削深度变化的趋势。当砂轮线速度和工件速度不变时,随着磨削深度的增加,工件表层的磨削温度升高,热应力作用明显,工件表层的塑形变形作用增大,比磨削能加大,因而工件表面残余应力增大。
从图可以看出,在乳化液条件下采用金刚石砂轮磨削TC4钛合金的工件表面残余应力均为残余压应力。其中,磨削深度对残余应力变化的影响最大,工件速度次之,砂轮线速度影响程度最低。综上,为了有效控制磨削后工件表面残余应力的大小,须合理选择磨削深度和工件速度,即尽可能选取较小的磨削深度,增大工件速度,保持砂轮的锋利,使材料的切除以切削为主,有效降低滑擦和耕犁作用,从而降低磨削区温度,减少热应力的影响,提高被磨工件表面的磨削质量。
4、结语
本文采用金刚石砂轮在乳化液条件下对TC4钛合金进行平面磨削试验,对比分析在不同粒度和磨削用量下的磨削表面粗糙度、显微硬度、工件表面层微观组织以及表面残余应力的变化规律,主要结论如下:
(1)在乳化液条件下,砂轮线速度和磨削深度对磨削表面粗糙度的影响显著,工件速度的影响不明显,因此可适当选取较大的工件速度,提高加工效率。实际加工中,在主轴功率和砂轮转速允许的情况下,尽量用较大的砂轮转速以达到较大的砂轮线速度,获得较好的表面粗糙度;采用较小的磨削深度可以获得较高的表面质量;同时采用较细粒度的砂轮加工可以获得较光滑的加工表面。
(2)从磨削参数对显微硬度的影响看:砂轮线速度提高,工件表面显微硬度减小;工件速度提高,工件表面显微硬度增大;磨削深度增大,工件表面显微硬度增大。磨削深度对工件表面显微硬度的影响最大,砂轮线速度次之,工件速度影响最不明显。
(3)从磨削参数对残余应力的影响看,在乳化液条件下采用金刚石砂轮磨削TC4钛合金的工件表面残余应力均为残余压应力。磨削深度对残余应力变化的影响最大,工件速度次之,砂轮线速度影响程度最低。所以要降低磨削后工件表面残余应力,合理选择磨削深度和工件速度,即尽可能选取比较小的磨削深度、适中的工件速度和相对较大的砂轮线速度。
(4)从工件表面层微观组织上看,砂轮粒度号越大,砂轮粒度越细,砂轮磨削的工件表面质量越好。
综上可知,采用金刚石砂轮在乳化液冷却条件下选择合适的磨削参数磨削TC4钛合金具有一定的可行性。
参考文献
[1]张利军,申伟,曹尔聪,等. 钛合金的磨削技术研究[J].工具技术,2013,47( 8) : 55 - 56.
[2]丁文锋,徐九华,杨长勇,等. 航空发动机零件高效精密磨削技术的发展与应用[J]. 航空制造技术,2014( 12) : 26 -29.
[3]韩野,崔海军. TC4 钛合金材料采用金刚石砂轮磨削时的工艺参数优化[J]. 航空制造技术,2015 ( 11) : 124 - 127.
[4]刘伟,邓朝晖,黄宇岑. TC4 钛合金高速外圆磨削表面完整性实验[J]. 宇航材料工艺,2017( 4) : 66 - 70.
[5]Naskar A,Choudhary A,Paul S. High speed moderate depth grinding of Ti-6Al-4V using monolayer CBN wheel[J]. Ad-vances in Materials and Processing Technologies,2018,4( 4) : 626 - 638.
[6]Chen Y G,Lu W Z,Xu J,et al. Investigation of surface integ-rity on TC4-DT in high speed grinding with CBN wheel[J].Advanced Materials Research,2014,27( 10) : 140 -145.
[7]肖鹏. 钛合金 TC4 超高速磨削表面完整性的研究[D].长沙: 湖南大学,2009.
[8]张昆鹏,王泽,刘蕴天. 磨削 T21 钛合金件表面质量的研究[J]. 当代化工研究,2017( 10) : 22 - 24.
第一作者: 方丁,高级工程师,成都飞机工业( 集团) 有限公司工程技术部,610073 成都市
First Author: Fang Ding,Senior Engineer,Chengdu Aircraft Industrial ( Group) Co. ,Ltd. ,LMT,Chengdu 610073,China
相关链接